Inhaltsverzeichnis
Hochleistungslaserschneiden ist ein hochmoderner Fertigungsprozess, der einen Laserstrahl mit hoher Energiedichte verwendet, um präzise und effizient durch verschiedene Materialien zu schneiden. Im Gegensatz zu traditionellen Schneidmethoden, die möglicherweise physischen Kontakt mit dem Material oder mechanische Werkzeuge erfordern, nutzt das Hochleistungslaserschneiden einen fokussierten Laserstrahl, um an der Schneidstelle intensive Hitze zu erzeugen, wodurch das Material effektiv verdampft, schmilzt oder ablatiert.
Vorteile des Hochleistungslaserschneidens
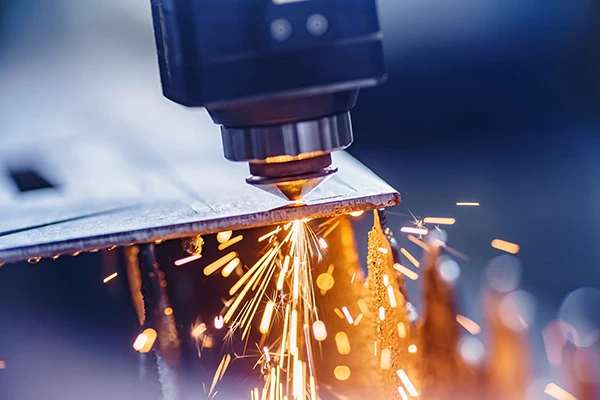
Hohe Schneidqualität
Der fokussierte Laserstrahl ermöglicht äußerst präzise und saubere Schnitte, was zu hochwertigen Endprodukten mit minimaler Verzerrung, Gratbildung oder rauen Kanten führt. Dies macht das Hochleistungslaserschneiden ideal für Anwendungen, bei denen Präzision und Oberflächenbeschaffenheit im Vordergrund stehen.
Hohe Effizienz
Hochleistungs Laserschneidmaschine bietet im Vergleich zu herkömmlichen Schneidausrüstungen schnelle Schnittgeschwindigkeiten und hohe Verarbeitungseffizienz. Die konzentrierte Energie des Laserstrahls ermöglicht eine schnelle Materialentfernung, was eine kosteneffektive Lösung für industrielle Fertigungsprozesse darstellt.
Kontaktloses Schneiden
Im Gegensatz zu mechanischen Schneidmethoden, bei denen physischer Kontakt zwischen Schneidwerkzeugen und dem Material besteht, ist das Hochleistungslaserschneiden ein kontaktloser Prozess. Dies eliminiert das Risiko von Werkzeugabnutzung, Kontamination oder Beschädigung empfindlicher Materialien und ermöglicht das Schneiden von komplexen Formen ohne zusätzliche Werkzeuge.
Verschiedene Materialien
Das Hochleistungslaserschneiden ist vielseitig einsetzbar und kann auf eine Vielzahl von Metallen, wie Stahl, Aluminium und Titan, Kupfer und mehr angewendet werden. Diese Vielseitigkeit macht es zu einer bevorzugten Wahl in Branchen wie Automobilbau, Luft- und Raumfahrt, Elektronik, Medizinprodukte, und darüber hinaus.
Anpassungsfähigkeit und Flexibilität
Insgesamt stellt die Hochleistungslaserschneidetechnologie eine hochmoderne Lösung für die Präzisionsfertigung dar, die eine überlegene Schnittqualität, Effizienz, Vielseitigkeit und Anpassungsfähigkeit in einer Vielzahl von Branchen und Anwendungen bietet.
Gängige Defekte und Lösungen beim Hochleistungs-Laserschneiden
Im Allgemeinen gehören wichtige Prozessparameter, die die Qualität des Schneidens beeinflussen, Schneidgeschwindigkeit, Laserleistung, Hilfsgas, Fokusposition, laser nozzles, und Materialeigenschaften dazu. Es ist zu erkennen, dass viele Faktoren den Laserstrahlschneidprozess beeinflussen. Bei unsachgemäßer Steuerung oder ungenauen Parametern wird die Schneidpräzision und -qualität stark beeinträchtigt.
Schauen wir uns die häufigsten Schneidfehler und Lösungen bei der täglichen Bearbeitung an.
1. Beim Schneiden von Kohlenstoffstahl mit Sauerstoff können einige häufige Probleme auftreten:
1.1 Das Streifenmuster auf der oberen Schicht und die Ziehlinien auf der unteren Schicht des Blechs sind beide übermäßig rau.
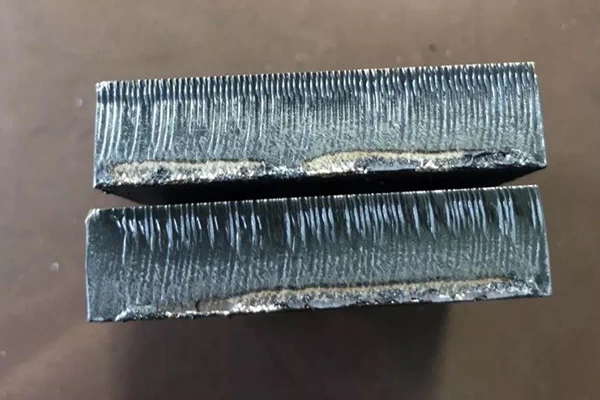
Mögliche Ursache:
- Düsenauswahl ist zu groß;
- Übermäßiger Schneiddruck führt zu Überbrennen;
- Die Schneidgeschwindigkeit ist zu langsam, was zu übermäßigem Brennen oder zu schnell führt, was zu unzureichendem Schneiden führt.
Lösung
- Kleine Düse durch geeignete Düse ersetzen;
- Den Luftdruck reduzieren, um eine hellere Schnittkante zu erhalten;
- Die Schneidgeschwindigkeit auf einen geeigneten Bereich für die aktuelle Leistung einstellen.
1.2 Die obere Schicht des Blechs zeigt leicht rauhes Streifenmuster mit geringfügigen oder tieferen Serrationen, während die untere Schicht bessere Ziehlinien aufweist.
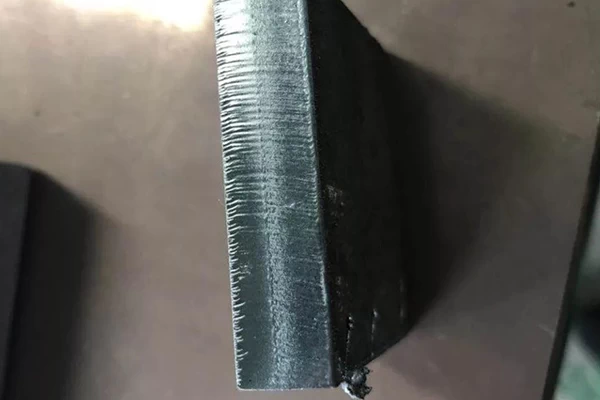
Mögliche Ursache:
- Düsenauswahl ist zu groß;
- Die Defokusmenge stimmt nicht überein;
- Langsamere Schneidgeschwindigkeit.
Lösung
- Kleine Düse durch geeignete Düse ersetzen;
- Bei gleichbleibendem Düsendurchmesser die positive Defokussierung weiter erhöhen;
- Die Schneidgeschwindigkeit auf einen für die aktuelle Leistung geeigneten Bereich einstellen.
1.3 Der obere Bereich des Blechschnitts zeigt gute Streifen, aber am Boden hängt Schlacke, was die Qualität des Schnitts beeinträchtigt.
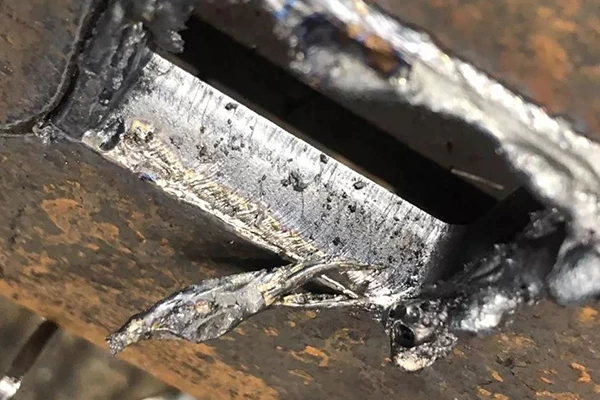
Mögliche Ursache:
- Der Vorwärtsdefokus ist zu groß, was dazu führt, dass die Energie konzentriert wird und ein nachhängendes Ende entsteht;
- Fehler bei der Luftdruckzufuhr: Zu geringer Luftdruck führt dazu, dass am Ende des Schnitts Ziehlinien und Schlacke entstehen;
- Zu schnelle Schneidgeschwindigkeit führt zu Nachhängen.
Lösung
- Die Vorwärtsdefokus angemessen reduzieren, die übrigen Parameter bleiben unverändert, die Schlackenbildung am Boden beobachten;
- Den Luftdruck angemessen erhöhen, versuchen, ihn maximal auf etwa 1 Bar zu erhöhen, und die Situation beobachten;
- Die Schneidgeschwindigkeit auf einen für die aktuelle Leistung geeigneten Bereich einstellen.
2. Beim Schneiden von Edelstahl mit Stickstoff können einige häufige Probleme auftreten:
2.1 Beim Schneiden von dünnen Edelstahlblechen können Delamination und raue Schnittflächen auftreten.
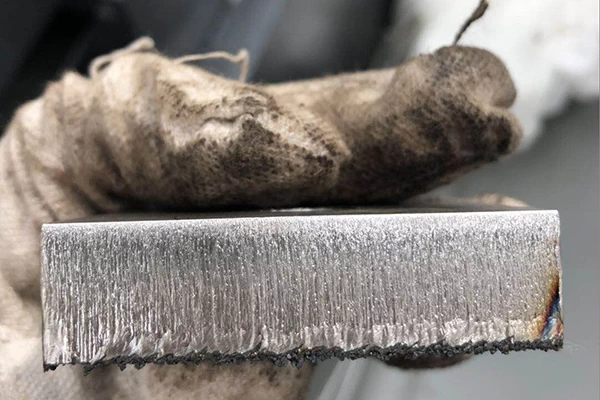
Mögliche Ursache:
- Die negative Defokusmenge ist zu groß, was zu Plasmabildung, Blaulichterzeugung und Schichtbildung führt;
- Düsendurchmesser ist zu klein;
- Luftdruckzufuhr ist zu groß.
Lösung
- Negative Defokus reduzieren, die übrigen Parameter bleiben unverändert, das Phänomen beobachten;
- Düsen durch größere Größen ersetzen;
- Luftdruckzufuhr angemessen reduzieren.
2.2 Beim Schneiden von dicken Edelstahlplatten treten unvollständige Schnitte auf. Der Schneideabschnitt erreicht nicht den Boden der Platte.
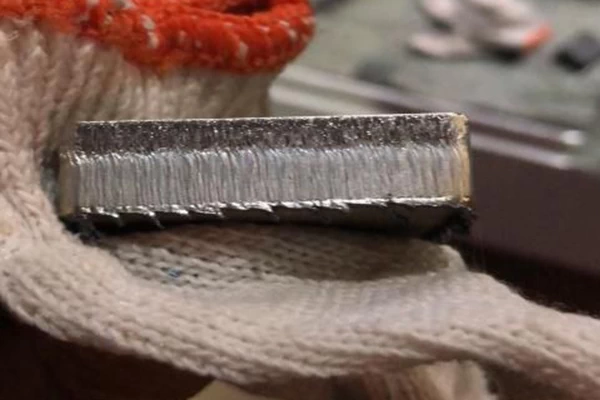
Mögliche Ursache:
- Die Düsenauswahl ist zu klein;
- Defokusmenge stimmt nicht überein;
- Unzureichender Gasdruck führt zu unzureichendem Schneiden.
Lösung
- Größere Düsen ersetzen, um den Gasfluss zu erhöhen;
- Negative Defokus weiter erhöhen, um den Schneideabschnitt zum Boden zu bringen;
- Luftdruck erhöhen.
2.3 Beim Schneiden von dicken Edelstahlplatten tritt Delamination auf, das Einstellen des Luftdrucks und der positiven / negativen Fokusmengen führt nicht zu einer signifikanten Verbesserung des Ergebnisses.
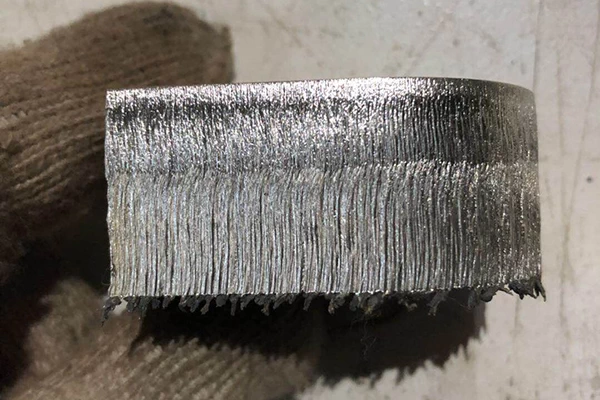
Mögliche Ursache:
- Wenn die Geschwindigkeit nicht erhöht werden kann, ist die Laserenergie zu konzentriert und die Reaktion mit dem Material zu heftig;
- Der Durchmesser der Düsenauswahl ist zu klein, was zu wenig Durchfluss führt.
Lösung
- Unter der Bedingung, dass die Spitzenleistung konstant bleibt, die Frequenz und den Tastgrad entsprechend reduzieren.
- Größere Düsen ersetzen, um den Gasfluss zu erhöhen.