Inhaltsverzeichnis
Mit der kontinuierlichen Entwicklung der Fertigungstechnologie wird die Laserschneiden technologie als effiziente und präzise Bearbeitungsmethode in der industriellen Produktion weit verbreitet eingesetzt. Um jedoch überlegene Laserschneideergebnisse zu erzielen, ist es wesentlich, mehrere Faktoren umfassend zu berücksichtigen und rational zu kontrollieren. Dieser Artikel wird verschiedene Faktoren untersuchen, die die Effekte des Laserschneidens beeinflussen, einschließlich der Laserleistung, des Laseroutput-Modus, der Position des Fokuspunktes, der Laserschneidgeschwindigkeit, des Schneidmaterials, des Hilfsgasdrucks und mehr.
Laserleistung
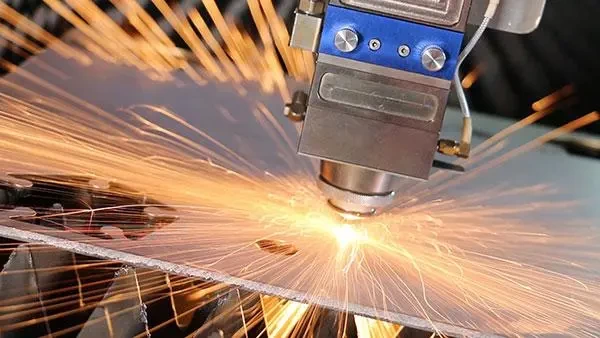
Die erforderliche Leistung für das Laserschneiden wird durch die Eigenschaften des Materials und den Schneidemechanismus bestimmt. Materialien mit hoher Oberflächenreflexion, guter Wärmeleitfähigkeit oder höheren Schmelzpunkten erfordern größere Laserleistung und Leistungsdichte. Unterschiedliche Schneidemechanismen für dasselbe Material können unterschiedliche Leistungsebenen erfordern. Die Verdampfungsschneidung erfordert die höchste Leistung, gefolgt von der Schmelzschnitt und die niedrigste Leistung wird für die sauerstoffunterstützte Schmelzschnitt benötigt. Mit zunehmender Dicke des Blechs steigt auch die erforderliche Laserleistung.
Laseroutput-Modus
Die Laserstrahlqualität wird in Einzelmodus und Mehrmodus, eingeteilt, wobei der Einzelmodus eine konzentrierte Energiedichte an einem einzigen Punkt aufweist, während der Mehrmodus zwei oder mehr konzentrierte Punkte aufweist. In Schneidanwendungen beeinflusst der Fokuspunkt maßgeblich die Qualität des Schnitts. Einzelmodus-Laser mit feineren Kernen haben eine überlegene Strahlqualität im Vergleich zu Mehrmodus-Lasern, die eine gaußsche Verteilung der Energie aufweisen und einen Peak bilden, der einem scharfen, kreisförmigen Berg ähnelt. Mehrmodus-Laser haben einen groben Kern und eine niedrigere Strahlqualität und bilden ein umgekehrtes, schalenförmiges 3D-Bild mit steileren Kanten.
Einzelmodus eignet sich für dünnere Bleche, während Mehrmodus in dickeren Blechen besser abschneidet. Der Vergleich von Einzelmodus und Mehrmodus ist jedoch nicht von intrinsischem Wert; es handelt sich um Konfigurationen von Faserlasersystemen. Es ist vergleichbar mit der Wahl zwischen einer Limousine und einem Geländewagen, wobei die Auswahl von den spezifischen Bearbeitungsbedürfnissen der Endbenutzer abhängt.
Fokuspunktposition
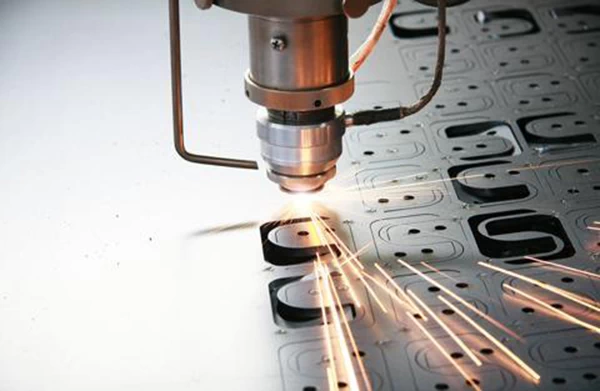
Die relative Position des Fokuspunkts zur Werkstückoberfläche ist entscheidend für die Sicherstellung der Schnittqualität. Üblicherweise liegt die Fokussierposition entweder genau an der Werkstückoberfläche oder leicht darunter während des Schneidens. Die Aufrechterhaltung einer konstanten relativen Position zwischen Fokus und Werkstück während des gesamten Schneidprozesses ist entscheidend für eine stabile Schnittqualität. Optimale Schneideergebnisse mit kleineren Schnittfugen und höherer Effizienz werden erzielt, wenn der Fokus in der bevorzugten Position liegt, oft knapp unterhalb der Düse. Der Abstand zwischen Düse und Werkstückoberfläche beträgt in der Regel etwa 1,5 mm.
Die Größe des fokussierten Laserstrahlspots ist direkt proportional zur Brennweite der Linse. Eine Linse mit kurzer Brennweite ergibt einen kleinen Spot mit hoher Leistungsdichte am Fokus, was für das Schneiden von Materialien vorteilhaft ist. Der Nachteil ist jedoch eine kurze Brennweite mit begrenztem Einstellspielraum, was sie für das Hochgeschwindigkeitsschneiden von dünnen Materialien geeignet macht. Im Gegensatz dazu bietet eine Linse mit langer Brennweite eine größere Fokustiefe, ausreichende Leistungsdichte, und eignet sich für das Schneiden von dicken Werkstücken.
Schneidgeschwindigkeit
Beim Laserschneiden beeinflusst die Schneidgeschwindigkeit maßgeblich die Qualität des geschnittenen Materials. Idealerweise wird eine Schneidgeschwindigkeit angestrebt, die auf der geschnittenen Oberfläche glatte Linien ohne geschmolzenen Schlacke darunter erzeugt. Wenn der Hilfsgasdruck und die Laserleistung konstant sind, zeigt die Schneidgeschwindigkeit eine nichtlineare inverse Beziehung zur Schnittfuge. Langsame Schneidgeschwindigkeiten führen zu einer längeren Laserenergiewirkung auf die Schnittfuge, was zu einer erhöhten Schnittfugenbreite führt. Übermäßig langsame Geschwindigkeiten erzeugen einen signifikanten Unterschied zwischen den oberen und unteren Schnittfugen, was zu einer verringerten Schnittqualität und einem erheblichen Rückgang der Produktivität führt.
Mit zunehmender Schneidgeschwindigkeit einer Metall-Laserschneidmaschine nimmt die Einwirkzeit des Laserstrahls auf das Werkstück ab. Dies verringert die Wärmeausbreitung und die Wärmeleitungseffekte, was zu einer entsprechenden Reduzierung der Schnittfugenbreite führt. Übermäßig hohe Geschwindigkeiten können jedoch zu unvollständigem Schneiden führen, da nicht genügend Schneidewärme eingebracht wird, was dazu führt, dass das Material ungeschnitten bleibt. Dieses unvollständige Schneiden-Phänomen, kombiniert mit dem Versäumnis, geschmolzenes Material rechtzeitig wegzublasen, führt zu einer Wiederanhaftung der Schnittfuge.
Schneidematerial
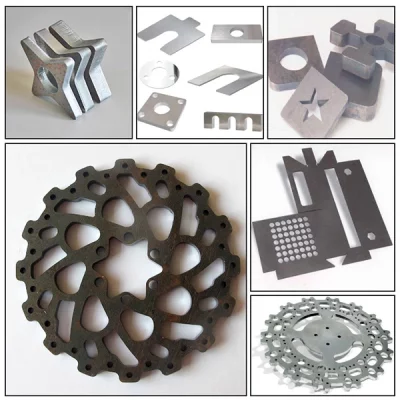
Die folgenden Faktoren haben den größten Einfluss oder bestimmen sogar, ob das Laserschneiden möglich ist, auf die Qualität des Laserschneidens:
Materialoberflächenreflexion
Nichtmetallische Materialien absorbieren im Allgemeinen gut für 10,6 mm Ferninfrarotstrahlen, die von CO2-Lasern emittiert werden, und zeigen hohe Absorptionsraten. Metallische Materialien mit hoher Reflexion, wie Gold, Silber, Kupfer und Aluminium, sind im Allgemeinen ungeeignet für CO2-Laserstrahlen, insbesondere für Dauerstrahlstrahlen, zum Schneiden.
Für Aluminium- und Kupfermetalle ist in der Regel eine Anfangsleistung von mindestens 3 kW erforderlich, um das anfängliche kleine Loch zu erzeugen, das für das Eindringen erforderlich ist. Materialien wie Stahl, Nickel und Titan zeigen eine gewisse Absorption des 10,6 mm CO2-Strahls, insbesondere wenn die Materialoberfläche auf eine bestimmte Temperatur erhitzt ist oder eine Oxidschicht aufweist, was zu deutlich verbesserten Absorptionsraten und besseren Schneideeffekten führt.
Für undurchsichtige Materialien gilt: Absorptionsrate = (1 – Reflexionsgrad), der von dem Zustand der Materialoberflächenbehandlung, der Temperatur und der Wellenlänge abhängt. Die Absorptionsrate des Materials spielt eine entscheidende Rolle im anfänglichen Erhitzungsstadium, aber sobald sich kleine Löcher im Werkstück bilden, macht der Schwarzkörper-Effekt der Löcher die Absorptionsrate des Materials nahezu 100%.
Materialoberflächenzustand
Der Oberflächenzustand des Materials beeinflusst direkt die Strahlabsorption, insbesondere die Oberflächenrauheit und die Oberflächenoxidschichten, was zu deutlichen Veränderungen der Oberflächenabsorptionsraten führt. In der Praxis des Laserschneidens wird der Einfluss des Oberflächenzustands des Materials auf die Strahlabsorptionsraten manchmal genutzt, um die Schneidleistung zu verbessern.
Hilfsgasdruck

Während des Laserschneidens spielen der Hilfsgasdruck Rollen wie das Wegblasen von geschmolzener Schlacke, das Kühlen des Materials und das Unterstützen der Verbrennung. Hilfsgasen gehören Sauerstoff, Druckluft, Stickstoff und Inertgase.
Sauerstoff kann an der Metallverbrennung beteiligt sein, was die Schneideffizienz verbessert, und eignet sich für das Schneiden der meisten Metalle. Inertgase und Luft sind für das Schneiden einiger Metallmaterialien (wie Aluminiumlegierungen) und nichtmetallischer Materialien geeignet, um eine Materialverbrennung zu verhindern.
Yupec Laser erinnert Sie daran, dass bei zu hohem Hilfsgasdruck Wirbel auf der Materialoberfläche auftreten können, was die Fähigkeit zur Entfernung von geschmolzenem Material beeinträchtigt und zu einer Zunahme der Schnittfugenbreite und rauen Schnittflächen führt. Ist der Druck zu niedrig, kann geschmolzenes Material nicht vollständig weggeblasen werden, was zu Materialhaftung und Schlackenbildung auf der Unterseite führt.
Daher ist es wichtig, den Hilfsgasdruck während des Schneidens anzupassen, um die beste Schnittqualität zu erzielen..
Laserdüse
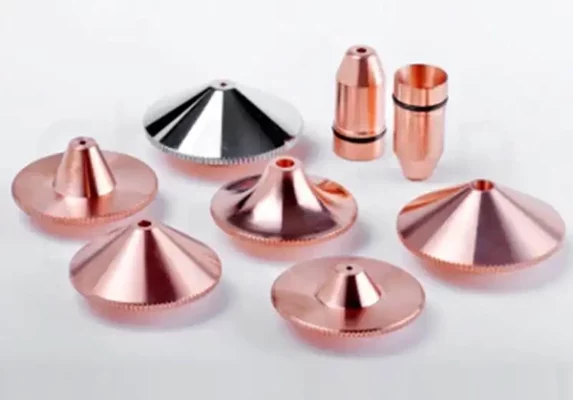
Die Laserdüse ist eine entscheidende Komponente, die die Qualität und Effizienz des Laserschneidens beeinflusst. Eine falsche Auswahl oder schlechte Wartung der Düse kann zu Verunreinigungen oder Beschädigungen führen. Unregelmäßigkeiten in der Rundheit der Düse oder lokale Blockaden durch thermisches Metterspritzen können zur Bildung von Wirbeln in der Düse führen und die Schneidleistung erheblich beeinträchtigen. Manchmal kann eine Fehlausrichtung zwischen der Düsenöffnung und der fokussierten Laserstrahlachse den Strahl am Rand der Düse abscheren, was sich auf die Schnittqualität auswirkt, die Schnittfugenbreite erhöht und zu Verschiebungen der Schnittdimensionen führt.
Zwei wesentliche Aspekte sollten bei Düsen berücksichtigt werden:
- Einfluss des Düsendurchmessers
- Einfluss des Abstands zwischen Düse und Werkstückoberfläche
Optisches Pfadsystem
Der vom Laser emittierte originale Laserstrahl wird durch das optische Pfadsystem (einschließlich Reflexion und Transmission) mit extrem hoher Leistungsdichte übertragen und beleuchtet die Werkstückoberfläche genau. Eine regelmäßige Inspektion und rechtzeitige Anpassung der optischen Komponenten im optischen Pfadsystem sind erforderlich, um sicherzustellen, dass der Strahl beim Durchlaufen der Schneidfackel über dem Werkstück korrekt zur Mitte der Linse übertragen und zu einem kleinen Spot fokussiert wird, um ein hochwertiges Schneiden zu ermöglichen. Änderungen oder Verunreinigungen der optischen Komponenten können die Schneidqualität beeinträchtigen und sogar das Schneiden unmöglich machen.
Verunreinigungen im Luftstrom und Spritzer, die an den optischen Pfadlinsen haften bleiben oder unzureichende Kühlung der Linse, können Überhitzung der Linsen verursachen, was sich auf die Energieübertragung des Strahls auswirkt. Dies kann zu einer Drift in der optischen Ausrichtung führen, was schwerwiegende Folgen haben kann. Überhitzung der Linse kann zu einer Verzerrung des Fokuspunkts und sogar zur Gefährdung der Linse selbst führen.
Zusammenfassung
Die Faktoren, die die Schneidqualität und -effizienz von Laserschneidemaschinen beeinflussen, umfassen die Laserleistung, den Ausgabemodus, die Fokusposition, die Schneidgeschwindigkeit, das Schneidmaterial, den Hilfsgasdruck, die Düse und das optische Pfadsystem. Um ausgezeichnete Schneideergebnisse zu erzielen, ist es notwendig, diese Faktoren umfassend zu berücksichtigen und eine präzise Steuerung umzusetzen. In Zukunft werden mit technologischer Innovation im Laserschneiden effizientere und intelligentere Lösungen erwartet, die neue Chancen für die Fertigungsindustrie bringen. Durch ein tiefes Verständnis und kontinuierliche Bemühungen können wir das Potenzial der Laserschneidetechnologie voll ausschöpfen und zuverlässige und effiziente Lösungen für die Präzisionsbearbeitung bereitstellen.