Índice de Contenidos
Con el continuo desarrollo de la tecnología de fabricación, la tecnología de corte láser se ha aplicado ampliamente en la producción industrial como un método de procesamiento eficiente y preciso. Sin embargo, para lograr resultados de corte láser superiores, es esencial considerar de manera integral y controlar racionalmente múltiples factores. Este artículo profundizará en varios factores que afectan los efectos del corte láser, incluida la potencia de salida del láser, el modo de salida del láser, la posición del punto focal, la velocidad de corte láser, el material de corte, la presión del gas auxiliar y más.
Salida de Potencia del Láser
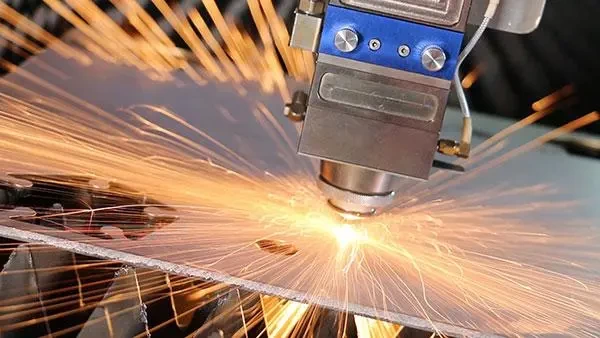
La potencia requerida para el corte láser se determina según las características del material y el mecanismo de corte. Los materiales con alta reflectividad superficial, buena conductividad térmica o puntos de fusión más altos demandan una potencia láser y densidad de potencia más grandes. Los diferentes mecanismos de corte para el mismo material pueden requerir niveles de potencia variables. El corte por vaporización requiere la potencia más alta, seguido del corte por fusión y la potencia más baja se necesita para el corte asistido por oxígeno. A medida que aumenta el grosor de la lámina, también lo hace la potencia láser requerida.
Modo de Salida del Láser
La calidad del haz láser se clasifica en modo único y modo múltiple, donde el modo único tiene una densidad de energía concentrada en un solo punto, mientras que el modo múltiple tiene dos o más puntos concentrados. En aplicaciones de corte, el punto de enfoque influye significativamente en la calidad del corte. Los láseres de modo único con núcleos más finos tienen una calidad de haz superior en comparación con los láseres de modo múltiple, que muestran una distribución gaussiana de energía, formando un pico que se asemeja a una montaña afilada y circular. Los láseres de modo múltiple tienen un núcleo más grueso y una calidad de haz más baja, formando una imagen 3D en forma de copa invertida con bordes más pronunciados.
El modo único sobresale en láminas delgadas, mientras que el modo múltiple funciona mejor en láminas gruesas. Sin embargo, comparar el modo único y el modo múltiple no tiene un valor intrínseco; son configuraciones de sistemas láser de fibra. Es similar a elegir entre un sedán y un vehículo todo terreno, donde la selección depende de las necesidades de procesamiento específicas de los usuarios finales.
Posición del Punto de Foco
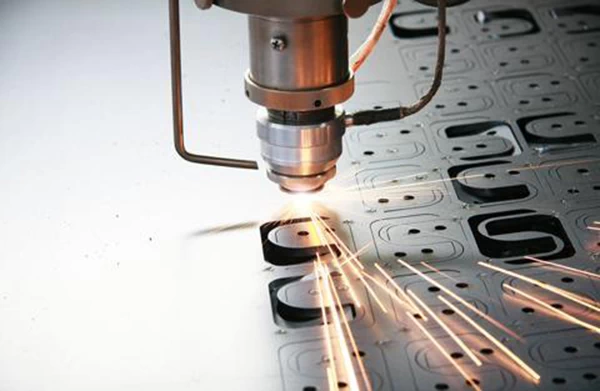
La posición relativa del punto de foco respecto a la superficie de la pieza es crucial para garantizar la calidad del corte. Por lo general, la posición del foco está justo en la superficie de la pieza o ligeramente por debajo de ella durante el corte. Mantener una posición relativa constante entre el foco y la pieza a lo largo del proceso de corte es vital para una calidad de corte estable. Se logran resultados de corte óptimos, con muescas más pequeñas y una mayor eficiencia, cuando el foco está en la posición preferida, a menudo justo debajo de la boquilla. La distancia entre la boquilla y la superficie de la pieza generalmente es de alrededor de 1.5 mm.
El tamaño del punto de haz láser enfocado es directamente proporcional a la longitud focal de la lente. Una lente de longitud focal corta produce un tamaño de punto pequeño con una alta densidad de potencia en el foco, lo que es beneficioso para cortar materiales. Sin embargo, la desventaja es una profundidad focal corta con un margen de ajuste limitado, lo que la hace adecuada para el corte de alta velocidad de materiales delgados. En contraste, una lente de longitud focal larga proporciona una profundidad focal más amplia, una densidad de potencia suficiente, y es adecuada para cortar piezas gruesas.
Velocidad de Corte Láser
En el corte láser, la velocidad de corte afecta significativamente la calidad del material cortado. Idealmente, se desea una velocidad de corte que produzca líneas suaves en la superficie cortada sin escoria fundida debajo. Cuando la presión del gas auxiliar y la potencia del láser son constantes, la velocidad de corte exhibe una relación inversa no lineal con el ancho de la ranura. Las velocidades de corte lentas resultan en una acción prolongada de la energía láser en la ranura, lo que lleva a un aumento del ancho de la ranura. Las velocidades excesivamente lentas crean una disparidad significativa entre las ranuras superiores e inferiores, lo que resulta en una calidad de corte reducida y una disminución sustancial en la eficiencia de producción.
A medida que aumenta la velocidad de corte de una máquina de corte láser de metal, el tiempo de acción del haz láser sobre la pieza de trabajo disminuye. Esto reduce los efectos de difusión del calor y la conducción térmica, lo que resulta en una reducción correspondiente del ancho de la ranura. Sin embargo, velocidades excesivamente altas pueden provocar un corte incompleto debido a la insuficiente entrada de calor de corte, haciendo que el material permanezca sin cortar. Este fenómeno de corte incompleto, combinado con la falta de eliminación rápida del material fundido, da como resultado la re-soldadura de la ranura.
Material de Corte
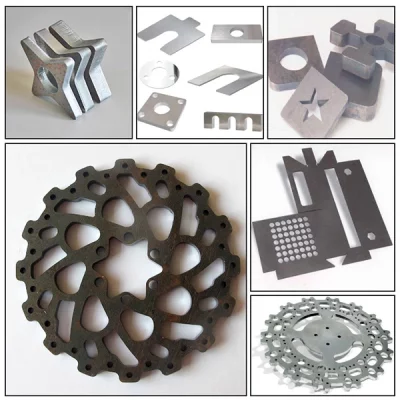
Los siguientes factores tienen el mayor impacto, o incluso determinan si el corte láser es posible, en la calidad del corte láser:
Reflectancia de la Superficie del Material
Materiales no metálicos generalmente absorben bien los haces de infrarrojo lejano de 10,6 mm emitidos por los láseres de CO2, mostrando altas tasas de absorción. Materiales metálicos con alta reflectividad, como oro, plata, cobre y aluminio, generalmente no son adecuados para los haces de CO2, especialmente los haces de onda continua, para el corte.
Para metales como aluminio y cobre, generalmente se requiere una potencia inicial de al menos 3 kW para crear el pequeño agujero inicial necesario para la penetración. Materiales como acero, níquel y titanio muestran cierta absorción del haz de CO2 de 10,6 mm, especialmente cuando la superficie del material se calienta a una cierta temperatura o tiene una película de óxido, lo que resulta en una mejora significativa de las tasas de absorción y mejores efectos de corte.
Para materiales opacos, la tasa de absorción = (1 - reflectancia), que depende del estado del tratamiento superficial del material, la temperatura y la longitud de onda. La tasa de absorción del material juega un papel crucial en la etapa inicial de calentamiento, pero una vez que se forman pequeños agujeros dentro de la pieza de trabajo, el efecto de cuerpo negro de los agujeros hace que la tasa de absorción del material sea cercana al 100%.
Condición de la Superficie del Material
La condición superficial del material afecta directamente la absorción del haz, especialmente la rugosidad superficial y las capas de óxido superficiales, lo que causa cambios notables en las tasas de absorción superficial. En la práctica de corte láser, el impacto de la condición superficial del material en las tasas de absorción del haz a veces se utiliza para mejorar el rendimiento de corte.
Presión del Gas Auxiliar

Durante el corte láser, la presión del gas auxiliar desempeña roles como soplar la escoria fundida, enfriar el material y ayudar en la combustión. Gases auxiliares incluyen oxígeno, aire comprimido, nitrógeno y gases inertes.
El oxígeno puede participar en la combustión del metal, mejorando la eficiencia de corte, y es adecuado para cortar la mayoría de los metales. Los gases inertes y el aire son adecuados para cortar algunos materiales metálicos (como aleaciones de aluminio) y materiales no metálicos, evitando la combustión del material.
Yupec Laser te recuerda que si la presión del gas auxiliar es demasiado alta, pueden aparecer vórtices en la superficie del material, debilitando la capacidad de eliminar el material fundido y causando un aumento en el ancho de la ranura y superficies de corte ásperas. Si la presión es demasiado baja, el material fundido no puede ser completamente eliminado, lo que conduce a la adherencia del material y la fijación de laescoria en la superficie inferior.
Por lo tanto, es esencial ajustar la presión del gas auxiliar durante el corte para lograr la mejor calidad de corte..
Boquilla Láser
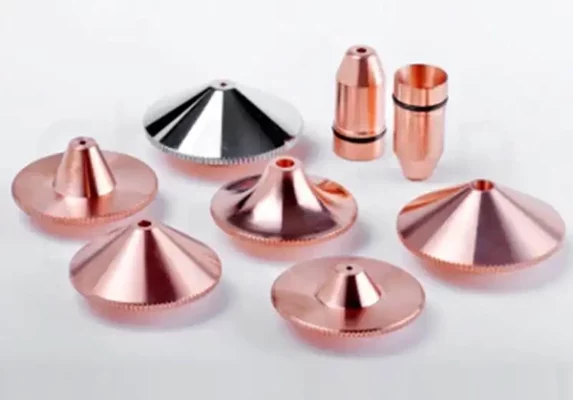
La boquilla láser es un componente crucial que afecta la calidad y eficiencia del corte láser. La selección incorrecta o el mantenimiento deficiente de la boquilla pueden causar contaminación o daños. Irregularidades en la redondez de la boquilla o obstrucciones locales debido a salpicaduras de metal térmico pueden provocar la formación de vórtices en la boquilla, degradando significativamente el rendimiento de corte. A veces, el desalineamiento entre la apertura de la boquilla y el eje del haz láser enfocado puede cortar el haz en el borde de la boquilla, afectando la calidad del corte, aumentando el ancho de la ranura y provocando desplazamientos en las dimensiones de corte.
Dos aspectos críticos deben considerarse para las boquillas:
- Influencia del diámetro de la boquilla
- Influencia de la distancia de la boquilla a la superficie de la pieza de trabajo
Sistema de Trayectoria óptica
El haz láser original emitido por el láser se transmite a través del sistema de trayectoria óptica (incluyendo reflexión y transmisión) con una densidad de potencia extremadamente alta, iluminando con precisión la superficie de la pieza de trabajo. La inspección regular y el ajuste oportuno de los componentes ópticos en el sistema de trayectoria óptica son necesarios para garantizar que cuando la antorcha de corte pasa por encima de la pieza de trabajo, el haz se transmita correctamente al centro de la lente y se enfoque en un punto pequeño, permitiendo un corte de alta calidad. Cualquier cambio o contaminación de los componentes ópticos puede afectar la calidad del corte e incluso hacer que el corte sea imposible.
Los contaminantes en el flujo de aire y las salpicaduras que se adhieren a las lentes de la trayectoria óptica o el enfriamiento insuficiente de la lente pueden causar sobrecalentamiento de las lentes, afectando la transmisión de energía del haz. Esto puede llevar a la deriva en la alineación óptica, lo que resulta en consecuencias graves. El sobrecalentamiento de la lente puede causar distorsión del punto focal e incluso poner en peligro la propia lente.
Conclusión
Los factores que influyen en la calidad y eficiencia del máquinas de corte láser incluyen la potencia de salida del láser, el modo de salida, la posición del punto focal, la velocidad de corte, el material de corte, la presión del gas auxiliar, la boquilla y el sistema de trayectoria óptica. Para lograr excelentes resultados de corte, es necesario considerar estos factores de manera integral e implementar un control preciso. En el futuro, con la innovación tecnológica, el corte láser presenciará soluciones más eficientes e inteligentes, brindando nuevas oportunidades para la industria manufacturera. A través de una comprensión profunda y esfuerzos continuos, podemos aprovechar plenamente el potencial de la tecnología de corte láser, proporcionando soluciones confiables y eficientes para el mecanizado de precisión.