Índice de Contenidos
La soldadura láser, como un método de soldadura con alta densidad de energía, se ha utilizado ampliamente en diversas industrias debido a sus ventajas como energía concentrada, alta precisión y buenos resultados. Sin embargo, con la expansión de sus aplicaciones, el problema de los poros generados durante la soldadura láser se ha vuelto cada vez más significativo. Estos poros no solo afectan la calidad de la soldadura, sino que también pueden provocar el fallo de la junta soldada. Para abordar mejor la ocurrencia de poros en la soldadura láser, se necesita un análisis exhaustivo de las razones de la formación de poros, junto con soluciones correspondientes, para garantizar la mejora de la calidad de la soldadura.
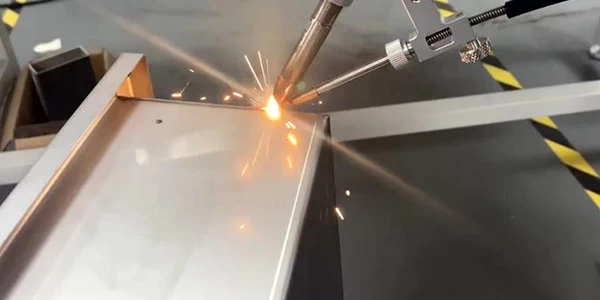
¿Por qué Ocurren Poros durante la Soldadura Láser?
Los poros son causados por la captura de gas durante el proceso de solidificación del metal de soldadura. La velocidad de enfriamiento rápida del metal de soldadura durante la soldadura láser, en comparación con la soldadura convencional, hace que sea difícil que los gases escapen de la soldadura, lo que lleva a la formación de poros.
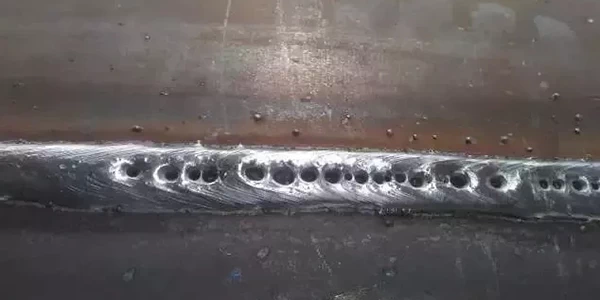
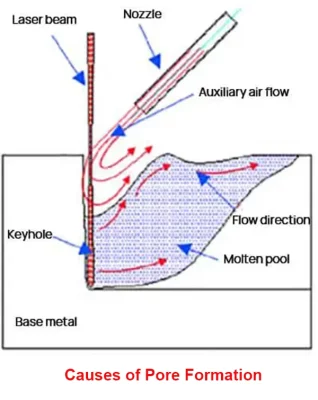
Causas de la Formación de Poros: Por un lado, debido a las limitaciones de las condiciones de sinterización y prensado , es imposible que los materiales metalúrgicos en polvo alcancen la misma densidad que los materiales fundidos. Por otro lado, los poros también son un defecto común en el proceso de soldadura láser. Debido a la influencia de la presión dinámica del gas auxiliar en el flujo del charco de fusión y el escape del gas en pequeños agujeros durante el proceso controlado de plasma fotoinducido, es un resultado directo de la soldadura de fusión profunda.
Métodos para Prevenir la Formación de Poros en la Soldadura Láser
La soldadura láser es un método de soldadura con alta densidad de energía, comúnmente utilizado para soldaduras de alta precisión y alta calidad. Sin embargo, pueden generarse poros durante el proceso de soldadura láser, lo que afecta la calidad de la soldadura. Aquí hay algunos métodos para resolver el problema de los poros al utilizar una máquina de soldadura láser:
Tratamiento de Superficie Pre-soldadura
Suprimir los poros de soldadura mediante la adopción de un tratamiento de superficie pre-soldadura. El tratamiento de superficie pre-soldadura es un método eficaz para controlar los poros metalúrgicos en las soldaduras láser de aleaciones de aluminio. Los métodos comunes de tratamiento de superficie incluyen limpieza físico-mecánica y limpieza química. Después de comparar, se obtienen los mejores resultados mediante el uso de un método químico para tratar la superficie de la pieza de prueba (limpieza con agente de limpieza de metal - lavado con agua - lavado con álcali - lavado con agua - lavado con ácido - lavado con agua - secado). El lavado con álcali utiliza una solución acuosa de NaOH (hidróxido de sodio) al 25% para eliminar el grosor de la superficie del material, y el lavado con ácido utiliza una solución acuosa de HNO3 (ácido nítrico) al 20% + 2% de HF (ácido fluorhídrico) para neutralizar el álcali residual. Después del tratamiento pre-soldadura, se recomienda limpiar la pieza de prueba con alcohol anhidro si se mantiene ensamblada durante un período prolongado.
Además, utilizando un medidor de limpieza de superficies, expresado en unidades RFU, se pueden detectar, cuantificar y registrar rápidamente datos relacionados con la limpieza de componentes. Basándose en estos datos, es posible evitar el impacto del juicio subjetivo y revisar de manera más efectiva los pasos de producción y los procedimientos de limpieza, optimizando así el proceso de limpieza, maximizando la eficiencia del trabajo, reduciendo las tasas de retrabajo y disminuyendo los costos de producción.
Control de Parámetros del Proceso de Soldadura
La formación de poros de soldadura está relacionada con la calidad del tratamiento de superficie del material y los parámetros del proceso de soldadura. La influencia de los parámetros de soldadura en la formación de poros de soldadura se refleja principalmente en la penetración de fusión de la soldadura, es decir, la influencia de la relación de ancho posterior de la soldadura en el poro. Los resultados de las pruebas muestran que cuando la relación de ancho posterior R > 0.6, puede mejorar eficazmente la distribución concentrada de poros en forma de cadena en la soldadura; cuando la relación de ancho posterior R > 0.8, puede mejorar eficazmente la presencia de grandes poros en la soldadura y eliminar en gran medida los poros residuales en la soldadura.
La potencia láser y la velocidad de soldadura afectan significativamente la formación de poros. Un estudio sobre la relación entre el número de poros y la potencia láser indica que a medida que aumenta la potencia láser, también aumenta el número de poros. Se especula que el aumento de la potencia calienta el metal fundido a una temperatura muy alta, generando vapor de metal, lo que hace que el metal líquido en el charco de fusión sea inestable y turbulento. Al reducir la potencia láser y aumentar la velocidad de soldadura, es posible reducir la formación de vapor de metal, suprimiendo así la formación de poros.
Es mejor realizar experimentos sistemáticos de optimización de parámetros de soldadura para encontrar la mejor combinación de potencia láser, velocidad, frecuencia de pulso y otros parámetros. Utilizando un sistema de retroalimentación en bucle cerrado, es posible ajustar automáticamente basándose en el monitoreo en tiempo real de las condiciones de la soldadura, mejorando la consistencia y calidad de la soldadura.
Selección Correcta de Gas de Protección
Como se muestra en la figura anterior, se utilizan gases de protección como Ar (argón) y He (helio) para proteger la superficie de la soldadura. En la soldadura láser de aleaciones de aluminio, Ar y He tienen diferentes grados de ionización cuando están expuestos a láseres, lo que da como resultado formaciones de soldadura diferentes. Los resultados muestran que utilizar Ar como gas de protección produce en general una menor porosidad de la soldadura en comparación con el uso de He como gas de protección.
También es importante tener en cuenta que un flujo de gas demasiado bajo (<10 L/min) puede generar una gran cantidad de plasma que no se puede eliminar, desestabilizando el charco de soldadura y aumentando la probabilidad de formación de poros. Un flujo de gas moderado (alrededor de 15 L/min) controla eficazmente el plasma, y el gas de protección cumple un buen papel en la prevención de la oxidación, lo que resulta en la menor porosidad. Un flujo de gas excesivo, acompañado de una presión de gas excesiva, introduce algo de gas de protección en el charco de fusión, aumentando la tasa de porosidad.
Por lo tanto, la elección del gas de protección afecta directamente la calidad, eficiencia y costo de la soldadura. En la soldadura láser, introducir correctamente el gas de protección puede reducir eficazmente la porosidad de la soldadura. Debido a la influencia de las propiedades del material, no es posible evitar completamente el fenómeno de soldaduras sin poros durante la soldadura, solo reducir la tasa de porosidad. Por lo general, el aluminio utiliza argón para reducir la tasa de porosidad, mientras que el acero inoxidable utiliza nitrógeno para reducir la tasa de porosidad.
Adopción del Método de Oscilación de la Viga
Al introducir una oscilación durante la soldadura, la oscilación recíproca de la corriente del haz hace que algunas soldaduras se vuelvan a fundir repetidamente, extendiendo el tiempo que el baño de soldadura permanece en estado líquido. Simultáneamente, la desviación del flujo del haz aumenta el calor de entrada por unidad de área, reduciendo la relación profundidad-ancho de la soldadura, facilitando el escape de burbujas y eliminando así los poros. Por otro lado, la oscilación de la corriente del haz hace que el pequeño orificio oscile junto con él, proporcionando una fuerza de agitación al baño de soldadura. Esto aumenta la convección y agitación del baño de soldadura, beneficioso para eliminar los poros.
Preheating and Post-heat Treatment
Para piezas de trabajo o materiales de soldadura sensibles, considere la precalefacción antes de la soldadura para reducir la humedad en el material. Además, el tratamiento post-calor puede ayudar a reducir el tamaño y la cantidad de poros.
- Control de Parámetros de Precalefacción:
En la etapa de precalefacción, asegúrese de utilizar la temperatura adecuada y el tiempo de retención para evitar el estrés térmico y los efectos de precalefacción desiguales. Utilice equipos de calentamiento auxiliares para garantizar que toda el área de soldadura reciba precalefacción uniforme.
- Optimización del Tratamiento Post-calor:
Para diferentes materiales y condiciones de soldadura, optimice la temperatura, el tiempo y otros parámetros del tratamiento post-calor para minimizar el tamaño y la cantidad de poros.
Monitoreo y Control
Implemente sistemas avanzados de monitoreo en tiempo real, que incluyan cámaras de alta velocidad, sensores y sistemas de adquisición de datos, para monitorear cualquier anomalía durante el proceso de soldadura. Combinado con un sistema de control inteligente, identifique y corrija problemas potenciales de manera oportuna, mejorando así la consistencia y estabilidad de la soldadura.
- Monitoreo de Alta Resolución:
Utilice sistemas de monitoreo de alta resolución, como cámaras de alta velocidad y sistemas de dispersión láser, para monitorear cambios sutiles durante el proceso de soldadura. Esto ayuda a detectar problemas potenciales de manera oportuna y tomar medidas para prevenir la formación de poros.
- Control de Aprendizaje Automático:
Combine algoritmos de aprendizaje automático para analizar y modelar datos de monitoreo en tiempo real, permitiendo que el sistema aprenda y prediga tendencias en la formación de poros. A través de un sistema de control inteligente, logre un control más preciso de la formación de poros.
Resumen
En resumen, las máquinas de soldadura láser han superado los desafíos tradicionales en la soldadura de materiales de cobre aprovechando ventajas como una alta densidad de energía, un control preciso y una pequeña zona afectada por el calor. Esto ha abordado eficazmente problemas como la alta conductividad térmica, la oxidación y los altos puntos de fusión que se encuentran en la soldadura de cobre. A medida que aumenta la demanda de materiales de cobre, la tecnología de procesamiento láser está lista para convertirse en un factor clave. Además, la aplicación de láseres de luz verde y azul abre nuevas posibilidades para el procesamiento láser de materiales de cobre, impulsando una nueva ronda de crecimiento en la industria del láser. Esta tendencia de desarrollo no sólo eleva el nivel del procesamiento de materiales de cobre, sino que también proporciona soluciones confiables y eficientes para el sector manufacturero moderno.