Table of Contents
When it comes to the modern field of sheet metal processing, laser welding technology has become an indispensable innovation, providing manufacturers with efficient and high-quality solutions. Handheld laser welding machine and automated laser welding machine are commonly used in sheet metal applications. This article primarily focuses on the application of handheld laser welding machine in sheet metal processing, exploring its characteristics, advantages, and a comparison with automated laser welding machine.
Overview of Handheld Laser Welding Technology
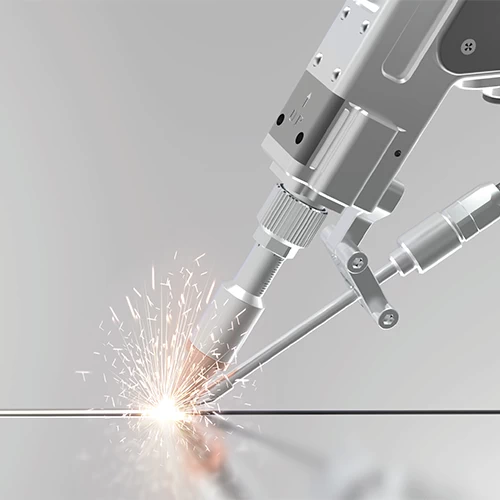
Handheld laser welding is a highly precise welding method that utilizes a laser beam to locally heat the material to its melting point and then rapidly cools it to accomplish the welding process. The working principles and machine of this technology mainly include a laser source, optical system, handheld device, and control system. Handheld laser welding machine is typically portable, allowing operators to weld at the required locations, making it highly useful in sheet metal processing.
Demands in the Sheet Metal Processing Industry
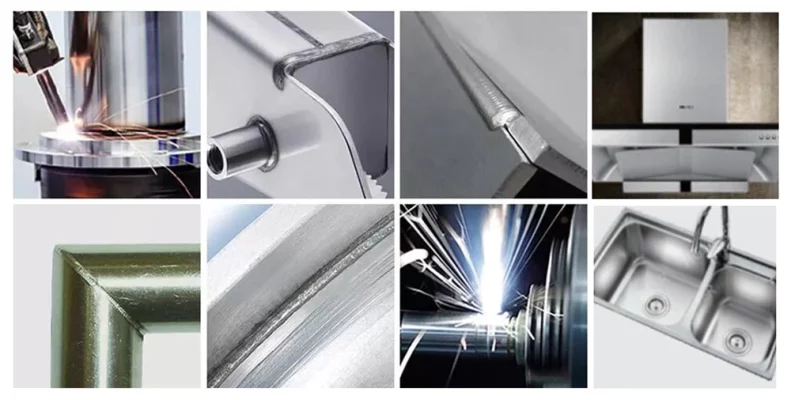
Sheet metal processing is a critical sector in manufacturing, covering the production of various products such as automobiles, electronic devices, home appliances, aerospace components, and more. As the requirements for welding strength and visual appearance in sheet metal welding continue to rise, especially for high-value components with stringent welding quality requirements, traditional welding methods that introduce significant heat input tend to result in problems like workpiece distortion and the need for extensive grinding and shaping, thus increasing costs. Laser welding, on the other hand, offers high energy density, a low heat-affected zone, significantly improving welding efficiency and quality while reducing post-welding processing time. Consequently, the application of laser welding in modern sheet metal manufacturing is becoming increasingly widespread.
In sheet metal manufacturing, different products have varying requirements for welding strength, visual appearance, and speed. Laser welding can achieve visually appealing, smooth, distortion-free welds. However, some components with internal structures or those intended for painting post-welding demand higher welding strength and welding speed. In this regard, handheld laser welding machines have a significant advantage, as they can not only achieve visually appealing conduction welding but also high strength and deep penetration welding at high speeds.
Characteristics of Handheld Laser Welding Machine
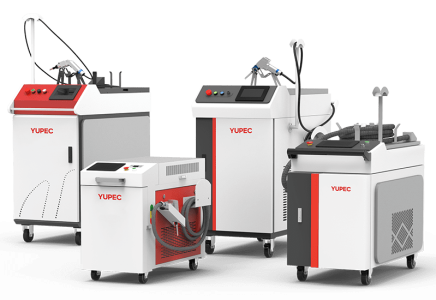
Handheld laser welding machine and automated laser welding machine are commonly applied in sheet metal processing. Most sheet metal enterprises mainly process materials such as thin sheets or medium-thickness sheets, including cold-rolled sheets, galvanized sheets, stainless steel sheets, and aluminum sheets. Handheld laser welding machine is an entry-level product suitable for sheet metal enterprises. It is a versatile laser welding device that requires minimal operator skill, making it suitable for regular welders. The machine is user-friendly, allowing for easy operation, even without the guidance of experienced experts. Compared to traditional methods like TIG welding and MIG welding, handheld laser welding offers faster welding speeds, controlled distortion, and aesthetically pleasing welds. In many cases, post-welding grinding or minimal grinding is not required.
In the past, it was commonly believed that laser welding was reserved for high-end processing requirements. However, with technological advancements, laser welding is expanding into new market segments, including welding for products like metal fences, bathroom fixtures, cabinets, enclosures, cabinets, and railings. These types of welding are often irregular, involve multiple small-batch orders, and do not require fixtures. Handheld laser welding is a versatile tool for these specialized market segments.
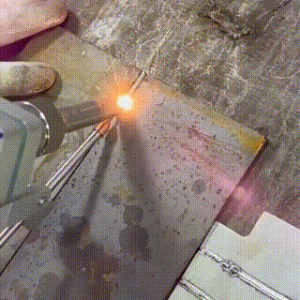
Handheld laser welding machine exhibits several key features in sheet metal processing:
- Flexibility and Maneuverability: Handheld laser welding machine is highly flexible, capable of adapting to various shapes and sizes of workpieces. Operators can freely move the machine to weld different locations, making it suitable for various work environments.
- Repairs and Detail Welding: Handheld devices are suitable for repair work and welding small parts in hard-to-reach places. They can precisely weld tiny components, making them ideal for fine work in sheet metal processing.
- Operator Skill: Compared to automated systems, handheld machine is easier to use and requires less training. Operators can manually adjust welding parameters as needed to meet different job requirements.
- Suitable for Small-Batch Production: Handheld machine is ideal for small-scale production, especially when personalized processing is required. It has a low initial cost, making it suitable for small and medium-sized enterprises or sheet metal workshops.
- Quick Setup: Handheld laser welding machine typically does not require complex setup and preheating processes. It can quickly start welding tasks, reducing production downtime.
- Flexible Welding Modes: Handheld devices often support various welding modes, including spot welding, continuous welding, pulse welding, and more, making them suitable for a variety of application needs.
- Low Maintenance Costs: Compared to complex automated systems, handheld laser welding machine typically has lower maintenance costs, as it does not involve large-scale automation systems that require maintenance.
- Safety and Environmental Friendliness: Handheld laser welding generates minimal heat input and smoke, reducing operator exposure risks and enhancing safety. It also features low noise levels, improving the working environment and reducing noise pollution. Since it does not consume consumable materials, it reduces resource waste and promotes environmental sustainability.
Handheld Laser Welding machine vs. Automated Laser Welding machine
Handheld laser welding machine is mainly used for welding various small-batch, thin-sheet sheet metal components. Users can choose machine power based on product material thickness and welding requirements. For large-scale production of sheet metal components, the choice of automated laser welding machine depends on factors such as order volume, material thickness, product welding structure, weld seam length, required welding depth, and welding joint consistency before welding.
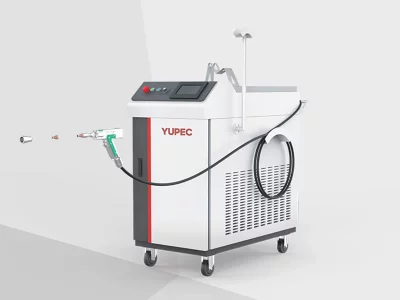
Handheld Laser Welding machine
Advantages:
- Flexibility and Maneuverability: Handheld laser welding machine is highly flexible, allowing operations to take place where needed, suitable for different positions on various workpieces.
- Suitable for Small-Batch Production: Handheld laser welding machine is an economical and efficient choice for small-scale production and repair work, as it does not require a large-scale automation system.
- Operator Skill: Handheld laser welding machine is user-friendly and requires minimal training. Welders with basic skills can operate it effectively and do not need experienced professionals for operation.
- Maintenance and Costs: Handheld laser welding machine is easier to maintain as it lacks complex automated systems and does not involve significant investments.
Disadvantages:
- Lower Production Efficiency: Handheld laser welding machine typically has slower production speeds and is not suitable for large-scale production requirements.
- Consistency: Manual operations may introduce variations due to operator skill differences, affecting welding quality consistency.
- Fatigue: Prolonged manual operation may lead to operator fatigue, potentially impacting welding quality and consistency.
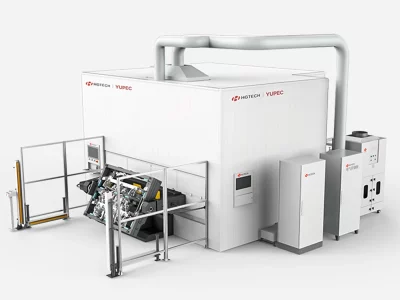
Automated Laser Welding machine
Advantages:
- High Production Efficiency: Automated laser welding machine generally offers high-speed welding capabilities suitable for large-scale production, improving production efficiency.
- Consistency and Precision: Automated laser welding systems provide a highly controlled welding process, eliminating the uncertainty introduced by manual operations and ensuring consistent welding quality.
- Suitable for Complex Geometries: Automated laser welding systems can weld complex sheet metal parts according to the program, eliminating the need for manual operations.
- Continuous Operation: Automated laser welding machine can run continuously without being affected by operator fatigue.
Disadvantages:
- High Costs: Automated laser welding systems typically require substantial investments, including equipment and system integration costs.
- Production Volume Constraints: Suitable for large-scale production but may not be ideal for small-batch production or rapidly changing requirements.
- Complexity: Automated laser welding systems require advanced programming and maintenance, along with specialized operator knowledge.
In summary, handheld laser welding machine is suitable for small-scale production, repair work, and flexible applications, offering advantages of flexibility and lower cost. Automated laser welding machine is ideal for large-scale production, offering increased production efficiency, consistency, and precision. However, it involves higher investments and specialized maintenance. The choice between these two options depends on production requirements, budget, and the nature of welding tasks.
Technical Challenges and Future Prospects
Although handheld laser welding technology has achieved significant success in sheet metal processing, it still faces several critical challenges. These challenges affect the widespread application of the technology, motivating researchers and manufacturers to continuously seek solutions. The following are some of the primary technical challenges:
- Cost Challenges: The purchase and maintenance costs of handheld laser welding machines are relatively high, potentially limiting adoption by some small and medium-sized enterprises. Reducing machine costs will be a future challenge to make the technology more accessible to a wider range of manufacturers.
- Material Compatibility: Not all materials are suitable for laser welding, especially highly reflective materials like aluminum and copper. Addressing this challenge requires ongoing research and innovation to expand the range of materials applicable to laser welding technology.
- Maintenance and Upkeep: Laser welding machine requires regular maintenance to maintain performance and accuracy. This includes cleaning optical systems, maintaining and calibrating laser sources. Enhancing machine stability and maintainability will be a crucial challenge.
- Safety: Laser radiation can pose risks to operators and the environment, necessitating effective safety measures and training to reduce hazards.
The continuous improvement and innovation of technology will drive progress in this field, bringing more opportunities and benefits to the manufacturing industry. The following are some essential points to consider regarding the future prospects of handheld laser welding technology:
- Technology Advancements: With ongoing technological advancements, laser welding machine will become more efficient, precise, and stable. New laser sources and optical systems will further improve welding quality.
- Cost Reduction: Lowering the cost of handheld laser welding machine is expected in the future, making it more accessible to small and medium-sized enterprises. Cost reduction will facilitate broader application.
- Material Innovation: Research into new material compatibility and applicability will drive the development of laser welding technology. Advances in materials science will expand its application areas.
- Automation and Intelligence: In the future, handheld laser welding machine will become more automated and intelligent. Automated systems will adapt to different workpiece shapes and sizes, further enhancing production efficiency.
- Sustainable Manufacturing: Laser welding technology holds significant potential for sustainable manufacturing and green production. Its precision and high material utilization reduce waste and energy consumption, contributing to environmental sustainability.
In conclusion, the future of handheld laser welding technology in sheet metal processing looks promising. Technological improvements, cost reduction, and automation will drive its widespread application while addressing safety and environmental challenges to ensure sustainable development. This will enhance the efficiency and product quality of the sheet metal processing industry, propelling manufacturing forward.
Conclusion
The application of handheld laser welding machine in sheet metal processing has achieved remarkable success, providing high-quality and efficient solutions to the manufacturing industry. The future of this technology is bright, particularly as it continues to evolve and improve. Handheld laser welding machine has become an indispensable tool in the sheet metal processing industry, and it will continue to play a vital role in enhancing product quality, improving efficiency, and advancing manufacturing. In the future, we can expect to see more innovations to address the challenges of handheld laser welding technology and expand its application areas. This will accelerate the development of the sheet metal processing industry and enhance the global competitiveness of manufacturing.