Table of Contents
Laser welding technology, as a highly advanced welding process, is continuously shaping the trends in the manufacturing industry. Its outstanding precision and high efficiency are gradually replacing traditional welding methods, making it the preferred welding process in many fields. However, it’s worth delving into the discussion of what materials laser welding machines can actually weld and how they perform concerning material characteristics.
Principles of Laser Welding
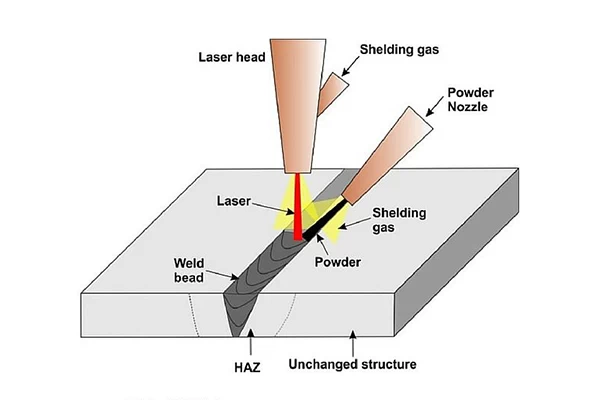
The core of laser welding is to precisely focus a high-energy laser beam on the welding material, causing it to reach high temperatures and melt instantly, and then quickly cool and solidify. This non-contact welding method in manufacturing provides products with higher quality and faster production speeds.
Key Features of Laser Welding Technology
High Weld Seam Quality
Laser welding produces high-quality weld seams because the laser beam allows precise control over the welding area, resulting in stable seam dimensions and shapes with minimal cracking and porosity.
Fast Welding Speed
The heating speed of laser welding is extremely fast, reaching several meters per second, leading to a rapid welding process.
Small Heat-Affected Zone (HAZ)
Due to the high heating speed and energy density of focused laser beams, the heat-affected zone is much smaller compared to traditional welding methods, resulting in relatively minor thermal impacts on the welding area.
Aesthetic Weld Seam Surface
Laser-welded seams have smooth surfaces, minimizing defects and providing an excellent visual appearance.
Materials Compatible with Laser Welding Machines
Metal Materials
Laser welding machines are suitable for welding various metal materials, including familiar ones like stainless steel, carbon steel, tool steel, galvanized sheet, copper, aluminum, gold, silver, titanium, nickel, tin, chromium, niobium, and alloys. Under certain conditions, laser welding can even join two different metal materials. Common shapes like dots, lines, circles, squares, right angles, and custom shapes can be welded in all directions, achieving spot welding, stack welding, seam welding, butt welding, seal welding, edge welding, and lap welding. The resulting weld points are fine, the seams are robust, and the workpiece deformation is minimal, requiring no grinding or polishing.
Stainless Steel
Generally, stainless steel welding is easier to achieve high-quality joints with laser welding than with traditional methods. The high welding speed and small heat-affected zone reduce overheating issues and the adverse effects of the large coefficient of linear expansion. Laser welding of stainless steel results in welds without defects like pores or inclusions. Compared to carbon steel, stainless steel, with its low thermal conductivity, high energy absorption rate, and efficient melting technology, can easily achieve deep narrow welds. Laser welding thin sheets with low power can produce joints with a good appearance and smooth weld seams.
Carbon Steel
Laser welding machines deliver good results when welding carbon steel, and the quality of the welding work depends on the impurity content. To achieve high-quality welding, preheating is necessary when the carbon content exceeds 0.25%. When welding steel materials with different carbon contents, the torch can be slightly tilted to the side of the low-carbon material to ensure joint quality.
Tool Steel
Laser welding is suitable for welding various tool steels, including S136, SKD-11, NAK80, 8407, 718, 738, H13, P20, W302, 2344, and others, with good welding results.
Copper and Copper Alloys
Copper and copper alloys tend to have issues with incomplete fusion and insufficient penetration. Therefore, concentrated energy and high-power heat sources, combined with preheating measures, should be employed. If there are no measures to prevent deformation in thin-walled or minimally rigid structures, welding can easily lead to significant deformations. When welding joint quality is subject to substantial rigidity constraints, welding stress may occur. Welding copper and copper alloys may also lead to thermal cracks, and porosity is a common defect in their welding.
Aluminum and Aluminum Alloys
The main challenge in laser welding aluminum is their high reflectivity to laser beams. Aluminum, being a good conductor of heat and electricity, has a high density of free electrons, making it an excellent reflector of light. The initial material surface reflectance exceeds 90%, meaning deep fusion welding must start with less than 10% of the input signal energy, requiring high input-output power to ensure the required power density for the start of welding work.
Magnesium Alloys
Magnesium alloys, with a density 36% smaller than that of aluminum, have garnered attention as high-strength materials. Experiments on the pulsed YAG laser and continuous CO2 laser welding of AZ31B-H244 alloy (Al < 3.27%, Zn 0.79%, thickness 1.8 mm) yielded optimal welding conditions of 0.8 kW, 5 ms, 120 Hz, and 300 mm/s. With a focal size of 0.42 mm, continuous CO2 laser welding technology produced a well-penetrated weld.
High-Strength Low-Alloy Steel
Laser welding of high-strength low-alloy steel can achieve joints with mechanical properties equivalent to the base material, as long as the selected welding parameters are appropriate. HY-130 steel, a typical low-alloy high-strength steel treated with quenching technology, has high strength and crack resistance. Using conventional welding techniques, the weld and heat-affected zone (HAZ) structure consists of coarse grains, some fine grains, and the original social structure. The toughness and cracking resistance of the joint are much lower than those of the base material. The metal organization of the weld and HAZ is particularly sensitive to the development of cold cracks under the welding state.
Laser Welding of Dissimilar Materials
Laser welding can be performed on dissimilar metals such as copper-nickel, nickel-titanium, titanium-aluminum, and low-carbon steel-copper under certain conditions. Laser welding can also be applied to ceramics, glass, composite materials, and more. Preheating is required when welding ceramics to prevent crack formation, usually preheated to 1500°C, followed by welding in the air using a long-focal-length focusing lens. To enhance joint strength, welding wire can be added. Welding metal matrix composite materials may lead to brittle phases, causing cracks and reducing joint strength. In thin-walled or minimally rigid structures without deformation control measures, significant deformation can occur after welding. When welding joints are subject to substantial rigidity constraints, welding stress may occur. Welding copper and copper alloys may also lead to thermal cracks, and porosity is a common defect in their welding.
Plastics
Laser welding machines can weld thermoplastic materials and thermoplastic elastomers. Commonly used plastics include polypropylene (PP), polycarbonate (PC), polyvinyl chloride (PVC), polyethylene terephthalate (PET), also known as polyester resin, and more. Laser welding machines can weld a wide range of plastic products, especially complex and delicate plastic products used in medical equipment, automotive manufacturing, 3C electronics, etc. Ordinary workers can operate them after learning, and the process is highly controllable, reducing heat damage and thermal deformation, with a welding speed several times faster than traditional welding. However, some materials are challenging to weld with lasers due to their difficulty in penetration, resulting in less-than-ideal welding effects, such as engineering plastics like polyphenylene sulfide (PPS) and liquid crystal polymers.
Electronic Components
Laser welding machines can weld complex-shaped parts and tiny components, making them suitable for welding and processing items like iron-ion batteries, lithium-ion batteries, electronic sensors, connectors, mice, mobile phones, especially products susceptible to damage during welding. The laser head of a laser welding machine can be adjusted at any angle according to the needs of the workpiece, allowing flexible access to the interior and special parts of the workpiece for welding. When combined with robotic arms, it can achieve automation or semi-automation.
Summary
In conclusion, laser welding technology, with its high precision and efficiency, has become a leading welding process in manufacturing. The technology performs well on both metal and non-metal materials, including stainless steel, aluminum alloys, plastics, and more. Its advantages, such as high weld seam quality, fast welding speed, and a small heat-affected zone, make it widely applicable across various industries, including electronic devices, tool steels, low-alloy high-strength steels, and more. With the ongoing development of laser technology, laser welding is expected to further drive the advancement of the manufacturing industry in the future.