Table of Contents
As manufacturing industries continue to advance, laser technology has gained widespread use as a novel and efficient tool. Particularly with the development of additive manufacturing and Industry 4.0, engineers can create more complex product designs that require strict tolerances. Laser processing can manufacture products with intricate features that are challenging or impossible to produce with traditional machining equipment, and laser cutting, in particular, provides clean cuts without burrs or heat effects on surrounding materials, eliminating the need for secondary finishing.
Laser technology finds extensive applications in industrial manufacturing, including automotive production, electronic product manufacturing, aerospace manufacturing, and more. In the automotive industry, laser welding technology is used for seamless welding of large body steel plates, enhancing the strength and crash resistance of car structures. In electronic product manufacturing, laser precision machining techniques are employed for processes such as drilling, cutting, and engraving, significantly improving product accuracy and production efficiency. In the field of medical device manufacturing, laser processes have become the preferred manufacturing technology for equipment manufacturers designing smaller and more advanced products.
1. Laser Cutting
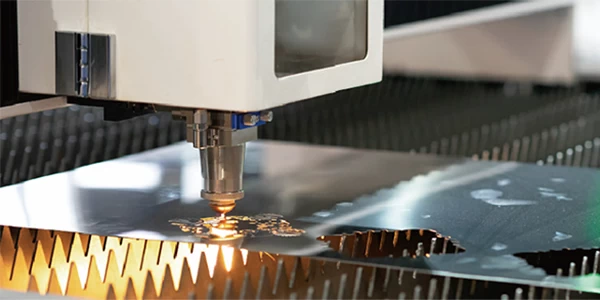
Laser cutting relies on a focused laser beam to precisely cut materials, creating straight cuts or patterns on materials or components to a very accurate depth. Fiber lasers are commonly used for processing various types of metals and polymers, as they can cut clean edges without generating a heat-affected zone. Laser cutting machines can be applied to various materials, including aluminum, titanium, and steel, achieving micron-level tolerances.
Robotic laser cutting is a multidirectional and multi-angle flexible cutting method implemented through industrial robots. Robotic laser cutting systems consist of a robotic arm, material positioner, robot controller, and end-of-arm tooling (EOAT). According to the latest research, robotic laser cutting machines are expected to show stable growth in the future market. However, product differentiation, cost reduction, and supply chain optimization remain crucial for the widespread adoption of robotic laser cutting machines. Market participants need to invest in research and development, establish strategic partnerships, and adjust their products based on evolving consumer preferences to leverage the significant opportunities presented by the robotic laser cutting machine market.
2. Laser Welding
Welding processes are particularly effective for connecting different materials with complex geometries or challenging joinability. In comparison to bonding or brazing, laser welding may be the preferred joining process, especially for connecting metals and plastics. It can create strong, high-precision welds, offering repeatable quality.
Laser welding is a fusion welding process where metals or thermoplastic materials are joined using a focused laser beam. It is an advanced welding process with applications across various industries, from aerospace and medical devices to fine jewelry production. During the welding process, a highly concentrated beam of light is focused on the cavity between the materials to be joined. The powerful laser beam liquefies the edges of the materials, merging them to form a seam. Due to the use of this highly concentrated heat source, laser welding can achieve high-speed welding of thin materials. In thicker materials, laser welding can produce deep and tight welds.
Advantages of laser welding include high speed – the execution speed is much higher than traditional techniques (approximately 4 times compared to TIG), and for some applications, it can reach 5000mm/min; non-contact – heat is transferred through the beam; high precision – even in cases of significant thickness differences, energy can be concentrated within a small area on both sides of the joint. The total amount of energy transferred is lower than TIG and MIG welding, reducing heat distortion and the need for cooling elements on the welding line.
Additionally, laser welding is suitable for a variety of materials, and by adjusting laser parameters, different materials, including copper and plastics, can be welded, forming weld joints of different sizes and depths. The aesthetic effect of laser-welded joints is comparable to professional TIG welding machines, but all operators can easily accomplish it, and the execution speed is faster. If the application allows, the grinding stage after welding can be omitted without sacrificing the aesthetic appearance of the product.
3. Laser Marking
Laser marking is increasingly used to imprint unique identification (UID) codes on components and products for easy tracking during recalls. For medical devices, laser marking is durable and can withstand multiple sterilizations. Marking includes readable information, barcode information, batch and lot codes, or even design history, and can be done with laser marking on products with flat or curved part geometries.
Between 2022 and 2027, driven by the increasing demand for precise and permanent marking solutions across various industries, the laser marking equipment market is expected to grow to $1.23 billion. The growth momentum in the market is projected to develop at a compound annual growth rate of 7.29% during the forecast period. Especially in emerging economies such as China and India, propelled by the expanding healthcare and food and beverage industries, which require precise coding of products during transportation.
Fiber laser marking, CO2 laser marking, UV laser marking, YAG laser marking, and diode laser marking are becoming prominent due to their versatility and efficiency. Laser engraving, laser etching, and laser coding are fundamental processes for various applications, including automotive, aerospace, medical devices, electronics, packaging, semiconductors, metals, plastics, glass, and wood.
Increasing demand for laser marking machines in other end-user industries is an emerging market trend. The demand for laser marking equipment increases across different industries. Laser marking was initially used for flat art and has now expanded into areas such as greeting cards, advertising, party accessories, and stationery.
The emergence of laser marking in packaging, especially in food and cosmetics, enhances the appearance of products and allows brands to stand out. With capacity growth and cost reduction, this technology will thrive in precision processing plants, boosting the demand for laser marking machines and promoting market growth.
Simultaneously, manufacturers of laser marking machines heavily depend on third-party suppliers for critical components, facing challenges such as quality issues, delivery delays, and strained relationships, affecting operations and cost efficiency.
4. Surface Texturing
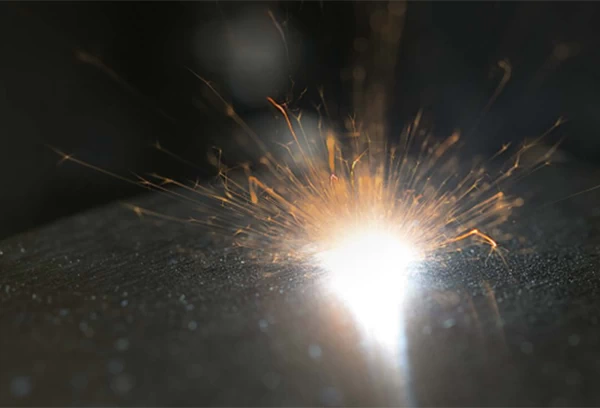
Laser technology can create textures or pattern microstructures on the surface of components or products, improving physical properties such as wear resistance, grip, optical performance, and load capacity. Laser micro-texturing can create roughness on medical implants, making it easier for new tissues or bones to adhere and grow into the new implant, and can achieve features as small as 10 micrometers with extremely high depth resolution.
Laser surface cleaning technology is no longer a novel technique and has found many applications in various industries. With the development of laser surface treatment technology, laser surface texturing techniques have also rapidly advanced. When surface texturing is performed using laser technology, roughness is achieved by the pulsed action of the laser beam removing material from the workpiece, creating craters and resulting in surface roughness.
For these purposes, pulsed fiber laser is used, which is best suited for this task. Surface roughening using laser technology also requires setting certain parameters to achieve different levels of roughness. Parameters affecting roughness include laser power, pulse repetition rate (PRR), scanning speed, and the focal length of the lens.
With laser technology, high-quality texturing can be applied to the surface of workpieces, and various levels of roughness can be achieved by adjusting parameters. A customizable set of parameters provides many possibilities for achieving different levels of roughness and complete control over the process. The main advantages of laser texturing include more precise processing, no need to mask other surfaces, process repeatability, no need for grinding media, the possibility of producing different textures in one step, and low operating and maintenance costs.
5. Laser Ablation
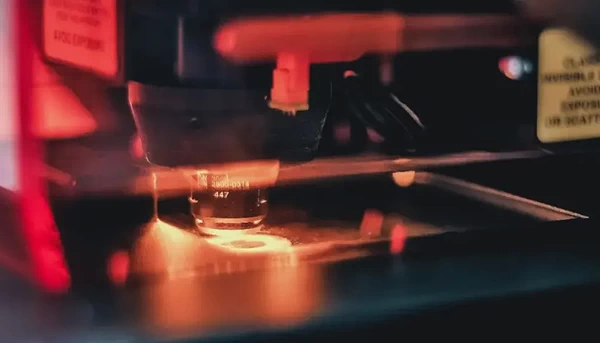
This “subtractive” machining method primarily involves the precise evaporation of materials using a laser beam. The pulse length, wavelength, and intensity can be adjusted according to the processing material. As this non-contact processing method does not change the material structure or damage the material surface due to wear or heating, it is particularly useful for sensitive materials such as nanomaterials or superconducting materials.
The increasing demand for miniaturized electronic components and the increasing adoption of laser technology in microelectronics manufacturing are driving the growth of the laser ablation system market. Meanwhile, advancements in laser technology, such as the development of ultrafast lasers and improvements in beam quality, are facilitating more precise and efficient material removal processes.
The application of laser ablation systems in medical device manufacturing, semiconductor manufacturing, and nanotechnology research will continue to increase, creating profitable opportunities for market participants. However, challenges related to strict regulations on safe use and environmental issues associated with laser ablation systems pose challenges to market growth.
The laser ablation system market can be segmented based on technology, applications, and end-users. By technology, the market can be divided into nanosecond laser ablation, picosecond laser ablation, and femtosecond laser ablation. By application, the market can include microprocessing, surface cleaning, paint removal, and others. End-user industries for laser ablation systems include healthcare, electronics, automotive, aerospace, research laboratories, and more.
6. Laser Drilling
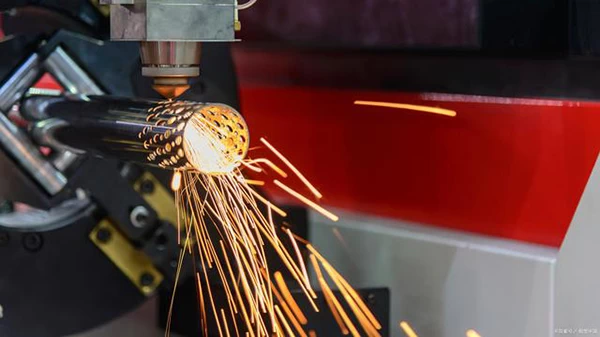
The precision of laser drilling micro-scale holes on materials such as metals, polymers, and ceramics is incredible. Many manufactured products today require tiny features that can only be achieved through laser drilling. Very small and complex features can be created on various materials through methods such as direct writing, perforation, and mask projection without generating heat effects or damaging materials.
Laser drilling is an extremely complex thermophysical process involving the interaction of lasers with matter. Therefore, there are many factors that affect the quality of laser drilling. To obtain high-quality holes, parameters affecting hole quality should be analyzed and understood based on the general principles and characteristics of laser drilling. These parameters include laser pulse energy, pulse width, defocusing, pulse repetition rate, and the characteristics of the processed material.
Repeatability, accuracy, flexibility, and cost-effectiveness are the main reasons why laser drilling is rapidly becoming popular as a processing technology. For flat metal parts, the advantages of punching are that many holes of even different sizes can be formed in one operation, facilitating the formation of parts with multiple holes in large batch production.
Laser technology eliminates the need and cost of manufacturing punching dies, providing a low-cost solution for prototypes or short-term parts. Laser drilling has no wearing or breaking parts, making it easy to process high-strength materials. Unlike mechanical punching, which has a diameter limit of approximately 1.0–1.5 times the thickness of the sheet metal, laser drilling offers tremendous flexibility in any hole formation operation.
7. Laser Wire Stripping
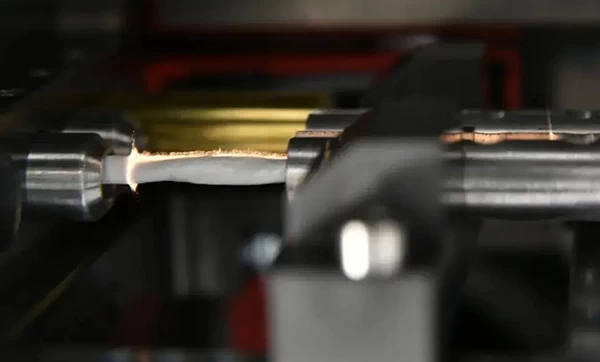
Laser wire stripping is a rapid process that offers excellent precision and process control while eliminating contact with the wire, allowing processing of precision wire sizes larger than 32 AWG. Stripping errors of the insulation layer can be controlled within 0.005 inches. Users can also program the stripping to ablate the insulation layer at any point on the conductor, achieving high-precision mid-section stripping.
The use of lasers to remove insulation or coatings from wires, conduits, and other medical devices is now commonplace. There are many advantages to using laser stripping processes in the manufacture of medical devices, with highly repeatable quality being the most important. Using a carbon dioxide laser to strip the polymer insulation from wire conductors, laser energy is easily absorbed by the insulation layer but highly reflected by the underlying metal conductor. Since the conductor reflects the laser, there is no risk of damage during stripping. Laser stripping can be applied to wires or cables of any shape, including circular, non-circular, flat ribbon, or any other shape. Stripping geometries include end stripping, window stripping, longitudinal cutting, or full-area ablation. The process is also very convenient for users. Unlike mechanical stripping methods, there is no need to change blades or consumables. The laser wire stripping process is non-contact, so there is no need for frequent replacement and maintenance.
The medical device manufacturing market requires high-quality processes and increasingly complex and precise wiring systems. Laser wire stripping can address many challenges in the industry, and as smaller and more delicate medical devices continue to develop, laser wire stripping will remain the preferred method.
Future Applications of Laser Technology
In conclusion, the importance of laser technology is becoming increasingly prominent, especially in the manufacturing sector. This method offers high precision, intelligence, and efficiency, with broad application prospects. In the future, this technology will be more widely used in other areas such as medical and security. Additionally, collaborative innovation and intelligent transformation will be important factors driving the advancement of laser technology. Yupec Laser will continue to innovate and research, promoting the widespread application of laser technology in manufacturing, healthcare, security, and other industries, playing a positive role in the transformation and upgrading of various industries.