Table of Contents
Laser welding has become a widely used welding process in many manufacturing fields. The technology of laser welding is constantly improving, and the process is becoming more sophisticated. So, what are the factors that affect the results of laser welding?
Welding Equipment
The performance of various welding equipment and its stability and reliability directly affect the welding quality. The more complex the equipment structure, the higher the degree of mechanization and automation, the welding quality is more dependent on it.
Therefore, such equipment is required to have better performance and stability. Welding equipment must be inspected and tried before use, and a regular inspection system must be implemented for all kinds of welding equipment in service.
For laser welding machines, the following aspects need to be paid attention to:
- Laser Types: Laser welding machines use either pulsed lasers or continuous lasers. The appropriate laser type should be selected based on the material being used.
- Beam Mode: A lower beam mode order indicates better focusing performance (i.e., better beam quality), resulting in a smaller spot size and higher laser power density for the same laser power, leading to a larger welding depth-to-width ratio.
- Output Power Stability: Better stability in the output power of the laser results in better welding consistency.
- Optical Transmission and Focusing Systems: These optical components may degrade under the influence of high-power lasers, causing a decrease in transmittance and generating a thermal lens effect (where the lens changes focus due to heating). Surface contamination can increase transmission losses or even damage optical components. Therefore, the quality, maintenance, and monitoring of optical components are crucial to ensuring welding quality.
In addition, the use of welding equipment conditions, such as the requirements of water, electricity, environment, etc., the adjustability of welding equipment, the space required for operation, error adjustment, etc. also need to pay full attention, so as to ensure the normal use of welding equipment.
Welding Workpieces

In order to ensure welding quality, quality inspection of raw materials is very important. In the initial stage of production, that is, before feeding materials, it is necessary to seal the materials in order to stabilize production and stabilize the quality of welded products.
- Absorption Rate of Material to be Welded: The compatibility of the laser beam with the material depends on important properties such as absorption rate, reflectivity, thermal conductivity, with absorption rate being the most critical. Some materials have excellent absorption rates for lasers, while others have poor or zero absorption.
- Uniformity of Material for Welding Workpieces: The uniformity of the material directly affects welding quality. For example, when welding aluminum alloys, uneven distribution of alloy elements or varying impurity content can lead to welding defects such as blowholes, undercutting, and craters. Non-uniform material dimensions, especially thickness and height, can result in poor fit with fixtures, deviations from the focal point, and suboptimal welding quality.
- Accuracy of Welding Workpiece Assembly: Due to the small size of the laser spot and narrow weld seam, welding typically does not involve adding filler metal. If the assembly has excessive gaps due to poor fit, the laser beam may pass through the gap without melting the base material or cause noticeable undercutting and craters.
- Cleanliness of the Workpiece to be Welded: Insufficient surface cleanliness with impurities can also lead to poor welding quality.
Welding Process Parameters
Welding process parameters include laser output power, welding speed, laser waveform, pulse frequency, defocus amount, and pulse width.
- Output Power: Laser welding involves a threshold energy density. Below this value, the melt depth is shallow. Once this value is reached or exceeded, the melt depth increases significantly. Plasma is generated only when the laser power density on the workpiece surface exceeds the threshold (related to the material), indicating the onset of stable deep penetration welding. If the laser power is below this threshold, only surface melting occurs, resulting in stable heat conduction welding. When the laser power density is close to the critical conditions for pore formation, the welding process becomes unstable, leading to significant fluctuation in melt depth. Laser power controls both the melt depth and welding speed during deep penetration welding. The melt depth is directly related to the power density of the incident beam and the focal spot size. In general, higher laser power leads to faster welding speeds, but excessively high power can cause the melt pool to be too deep, resulting in defects such as cracks. Therefore, it is recommended to prioritize determining the effective power range for better parameter adjustment during the tuning process.
- Welding Speed: Higher welding speeds result in shallower melt depths. A large and wide melt pool is formed at low speeds, making it prone to collapse. When welding at high speed, the intense flow of liquid metal in the center of the weld pool solidifies on both sides of the weld before having a chance to redistribute, resulting in an uneven weld seam. Therefore, Yupec Laser recommends using high-speed welding for thin plates or materials with good weldability and lower speeds for thick plates and challenging materials.
- Laser Waveform: Laser waveforms include pulse waveforms commonly used for pulsed lasers and seam welding waveforms for continuous welding. For example, when welding high-reflectivity materials such as copper, aluminum, gold, or silver, a trapezoidal laser waveform can be used to overcome the barrier of high reflectivity. For black metals like iron and nickel with low surface reflectivity, rectangular waves or gradually attenuating waveforms are preferable.
- Pulse Frequency: Pulse frequency, beam size, and welding speed must be matched to achieve the desired overlap rate. In general, a larger overlap rate results in a smoother weld, but the welding speed also decreases accordingly. When the laser pulse frequency exceeds a certain value, the overlap rate becomes too high, surpassing the material’s welding limit and leading to penetration or weld spatter.
- Defocus Amount: There are two types of defocusing: positive defocusing and negative defocusing. Positive defocusing places the focal plane above the workpiece, while negative defocusing places it below. With negative defocusing, the internal power density of the material is higher than on the surface, making it prone to stronger melting and vaporization, allowing the light to penetrate deeper into the material. In practical applications, negative defocusing is used when a large melt depth is required, while positive defocusing is suitable for welding thin materials.
- Pulse Width: This parameter mainly applies to pulse laser welding machines. Pulse width is one of the important parameters of pulse laser welding machines. It distinguishes between material removal and material melting and is a key parameter that determines the cost and volume of processing equipment. A longer pulse width results in a larger weld diameter, and for the same working distance, a deeper melt depth.
Worktable
The worktable directly influences the welding effect and processing efficiency. If the welding platform is not level or not vertical, the quality of the weld seam will be affected. Additionally, if the welding platform surface contains impurities such as oil and dust, these impurities can mix into the weld seam during the welding process, affecting the density and strength of the weld. In large-scale production, fully automatic laser welding machines often use automatic worktables to improve production efficiency, so the difference in worktables can have a significant impact on welding results.
Welding Fixtures
Welding fixtures ensure the precise positioning and secure clamping of welded components, facilitating the installation and welding of components and meeting the process requirements for structural accuracy. Actively promoting and applying fixtures that are compatible with product structures in modern welding production plays a crucial role in enhancing product quality, reducing labor intensity for workers, and accelerating the mechanization and automation of the welding process.
Protective Gas
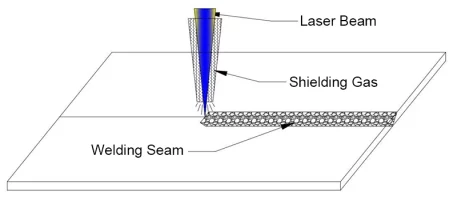
Protective gas, or shielding gas, is also one of the important factors affecting welding quality. Protective gas is an inert gas used to protect the molten pool during the laser welding process. Some materials may not require protective gas if surface oxidation is not a concern, but it is generally needed for most applications. Protective gas serves various purposes, such as expelling or weakening plasma (which is easily generated during laser welding and has effects on laser absorption, refraction, and reflection), increasing the cooling rate of the weld seam, reducing the degree of surface oxidation in the weld seam, and improving the surface appearance of the weld. Commonly employed protective gases include nitrogen, argon, helium, as well as mixtures of argon and helium. For more information about shielding gas in laser welding, you can see here.
Conclusion
In conclusion, the effectiveness of laser welding is influenced by a myriad of factors, ranging from the characteristics of the welding equipment to the intricacies of the welding process and the quality of the workpieces involved.
Selecting the appropriate laser type, ensuring stability in output power, and maintaining the integrity of optical components are critical considerations in welding equipment. The properties of the materials being welded, such as absorption rate, uniformity, and cleanliness, play a pivotal role in determining the overall welding quality.
Fine-tuning welding process parameters, including output power, welding speed, laser waveform, pulse frequency, defocus amount, and pulse width, is essential for achieving the desired welding results. Moreover, the condition of the worktable, the use of suitable welding fixtures, and the application of protective gas further contribute to the overall success of the laser welding process.
As laser welding technology continues to advance, understanding and optimizing these factors will be key to pushing the boundaries of precision, efficiency, and quality in various manufacturing applications. The intricate interplay of these elements underscores the importance of a holistic approach to laser welding, where careful consideration of each factor collectively contributes to the success of the welding process and the quality of the final product.