Table of Contents
Laser welding primarily targets the welding of thin-walled materials and precision components. It can achieve spot welding, butt welding, overlay welding, and hermetic welding. Laser welding offers a high depth-to-width ratio, narrow weld seams, a small heat-affected zone, minimal distortion, fast welding speeds, smooth and aesthetically pleasing welds, post-welding minimal or simple processing, high weld quality with no porosities, precise control, a small focal point, high positioning accuracy, and ease of automation.The key to achieving these remarkable outcomes lies in the often-overlooked factor of shielding gases.
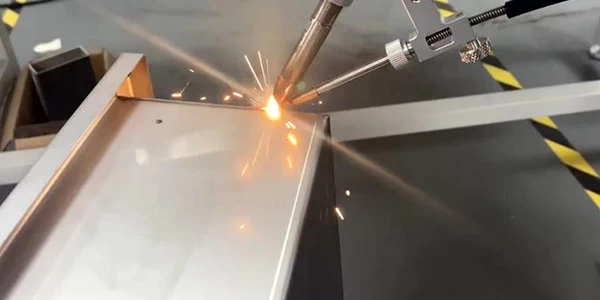
Shielding gases, despite their often inconspicuous presence, play a pivotal role in laser welding. These gases are specifically chosen to create a controlled environment around the welding area. They serve multiple critical functions that directly influence the overall quality, efficiency, and cost-effectiveness of the welding process.
The Role of Shielding Gas
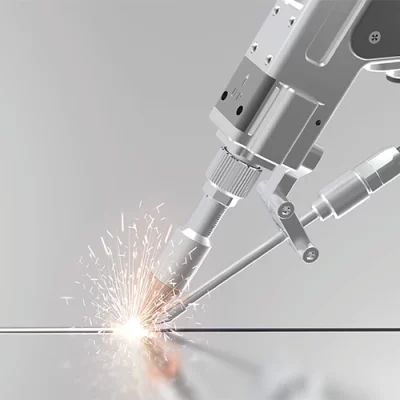
In laser welding, shielding gas plays a crucial role and affects the weld seam’s formation, weld seam quality, penetration depth, and width. Shielding gas serves several purposes in laser welding:
- Protection of the weld pool: Proper shielding gas introduction effectively protects the molten pool, reducing or preventing oxidation.
- Reduction of spattering: Correct shielding gas flow minimizes spatter formation during the welding process.
- Uniform bead formation: Adequate shielding gas flow ensures even spreading of the weld seam as the weld pool solidifies, resulting in a uniform and aesthetically pleasing weld.
- Reduction of plasma cloud interference: Properly introduced shielding gas minimizes the shielding effect of metal vapor plumes or plasma clouds, increasing the effective utilization of the laser beam.
- Pore reduction: Appropriate shielding gas flow helps reduce the formation of pores in the weld seam.
The correct choice of gas type, gas flow rate, and introduction method can yield ideal results. However, improper use of shielding gas can negatively impact the welding process.
Adverse Effects of Improper Shielding Gas Usage
While shielding gas typically has a positive impact on the weld seam, it can have adverse effects in some cases:
- Deterioration of weld quality: Incorrect shielding gas introduction can lead to poor weld seam quality.
- Crack formation: Choosing the wrong gas type may result in weld seam cracking and a decrease in mechanical properties.
- Oxidation: Incorrect gas flow management can lead to increased oxidation of the weld seam, potentially causing uneven formation or weld seam collapse.
- Ineffective shielding: Wrong gas introduction methods can compromise the protective effect, offering little or no protection to the weld seam.
- Reduced penetration depth: The introduction of shielding gas can affect the penetration depth of the weld seam, particularly in thin sheet welding.
Types of Shielding Gases
The main shielding gases used in laser welding are N2, Ar, and He. Their physical and chemical properties vary, and they have different effects on the weld seam:
- N2 (Nitrogen):Nitrogen ionizes moderately under the influence of laser treatment, reducing the formation of plasma clouds and improving the effective utilization of the laser beam. It can react with aluminum alloys and carbon steel, leading to increased brittleness and reduced toughness in the weld seam. However, it can strengthen the weld joint when welding stainless steel.
- Ar (Argon): Argon has a relatively low ionization energy, leading to higher ionization levels under the influence of laser, which can be less favorable for plasma cloud control but is non-reactive with common metals. Its density helps protect the weld pool and is commonly used as a shielding gas.
- He (Helium): Helium has the highest ionization energy, allowing excellent control of plasma cloud formation and offering efficient laser action on metals. Helium is non-reactive with metal structures, making it a good shielding gas. However, it is cost-prohibitive for high-volume production and is often used in scientific research or high-value products.
- Gas Mixtures: Many laser welding applications benefit from customized gas mixtures tailored to specific requirements. These mixtures can combine argon, helium, oxygen, and other gases in precise proportions to achieve the desired results.
Blowing Methods of Shielding Gas
The blowing method of shielding gas plays a key role in the welding and cutting process. Two common methods are side-axis blowing of shielding gas and coaxial blowing of shielding gas. These two methods vary based on where and how the gas is injected, and are used in different types of laser welding and cutting applications.
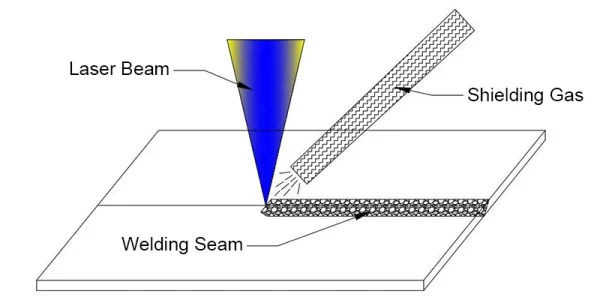
Side-Axis Blowing of Shielding Gas
- In side-axis blowing of shielding gas, the shielding gas is blown from the side of the welding area at a side angle. This is usually achieved through specially designed gas nozzles or nozzle assemblies.
- The main advantage of side-axis blowing shielding gas is that it can guide the gas directly to the welding area to prevent external air and impurities from entering the welding area. This helps reduce oxidation and provides better weld quality.
- This method is suitable for applications that require shielding gas to be concentrated in the welding area, especially when high weld quality requirements are required.
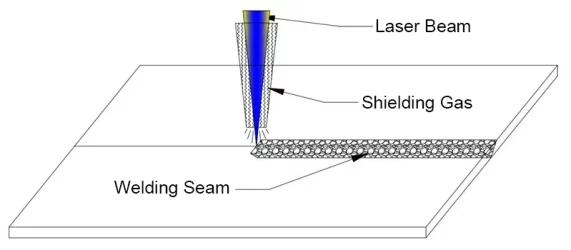
Coaxial Blowing of Shielding Gas
- Coaxial blowing of shielding gas is a method in which the shielding gas and the laser beam enter the welding area along the same axis. This is usually achieved in the nozzle of the laser welding head.
- The main advantage of coaxial blowing of shielding gas is that it can maintain the atmosphere around the welding area, prevent the entry of external air, and effectively protect the welding area. This helps reduce oxidation and improves weld quality.
- This method is suitable for applications where the laser beam and shielding gas need to be aligned to obtain high-precision and highly controlled welding.
The choice between side-axis blowing shielding gas or coaxial shielding gas usually depends on the specific welding process, materials and required welding quality. For applications requiring higher weld quality, protection against oxidation and interference from external impurities, side-axis blowing of shielding gas may be a better choice. In contrast, coaxial blowing of shielding gas is more suitable for welding applications that require high precision and control, as it ensures accurate alignment of the laser beam and gas flow. Regardless of the method, the correct shielding gas injection method is critical to obtaining high-quality laser welding and cutting results.
Selecting the Right Shielding Gas
Selecting the appropriate shielding gas is crucial for the success of the laser welding process. Different applications and materials require different types of shielding gases to ensure welding quality and efficiency. Several key factors should be considered when choosing the right shielding gas:
- Material Type: Different materials require different shielding gases. For stainless steel welding, argon is typically used as the shielding gas. Aluminum and aluminum alloys can benefit from pure argon or argon-helium mixtures. Ensuring compatibility with the welding material is essential.
- Sensitivity to Oxidation: Some materials are more susceptible to oxidation and require more protection. In such cases, high-purity inert gases, like argon, are usually the best choice to minimize oxygen presence and prevent material oxidation.
- Application Requirements: Different applications may have varying demands for welding quality and speed. Some may require high-speed welding, while others prioritize weld seam quality and appearance. Select the gas type and flow rate based on application requirements.
- Gas Mixtures: In some cases, gas mixtures can provide superior performance. Gas mixtures typically combine inert gases with active gases in precise proportions to meet specific needs, offering better atmosphere control.
- Cost Considerations: The cost of shielding gas is also a significant factor. Some gases are more expensive than others, and a balance must be struck between protecting welding quality and cost savings. In some cases, lower-cost gases can be used as auxiliary shielding gases to reduce expenses.
- Gas Purity and Quality: The purity and quality of shielding gas are crucial. Low-quality or contaminated shielding gas can adversely affect welding quality. Ensuring the use of high-quality and pure shielding gas is essential. Regular inspection and maintenance of the gas supply system are necessary to maintain purity and quality.
- Process Parameters: Select the appropriate shielding gas based on specific laser welding process parameters such as power, focus, speed, and welding mode. These parameters influence shielding gas flow and distribution.
When choosing the right shielding gas, it’s important to consider the factors mentioned above and conduct experiments or tests if necessary to determine the optimal configuration. Different welding applications and scenarios may require different shielding gas strategies. Collaborating with professional laser welding engineers or technical experts and suppliers can help ensure that the selected shielding gas meets specific requirements and delivers excellent welding results.
Supply and Control of Shielding Gas
Proper supply and control of shielding gas are critical aspects of the laser welding process. Ensuring correct supply and control helps maintain the appropriate atmosphere in the welding area, preventing oxidation and impurities from entering and, thus, ensuring welding quality and efficiency. Here’s some vital information about the supply and control of shielding gas:
- Gas Supply System: Shielding gas is typically stored in gas cylinders, including high-pressure and low-pressure cylinders. The gas source can be either gas cylinders or gas generators, depending on requirements. Piping systems transport gas from the cylinders or source to the welding equipment.
- Gas Flow Control: Accurate control of gas flow is crucial to ensure the right atmosphere. Flow rates are usually expressed in liters per minute (L/min) or cubic feet per hour (cfh). Precise flow control ensures the correct amount of gas flows into the welding area.
- Gas Pressure Control: Gas pressure also needs to be controlled. Gas pressure can be managed through pressure regulators or reducing valves to ensure gas enters the welding equipment and the welding area at the appropriate pressure.
- Gas Distribution and Guidance: Shielding gas should be correctly distributed in the welding area to ensure consistent protection throughout the welding process. Equipment such as nozzles, nozzle components, and gas conduits are used to guide gas flow into the welding area.
- Gas Control Systems: In highly automated laser welding systems, gas control systems are crucial. These systems monitor gas flow, pressure, and atmosphere and can automatically adjust to ensure a stable gas supply.
- Gas Purity: Gas purity is a critical factor. Low-quality or contaminated shielding gas can affect welding quality. Therefore, using high-quality and pure shielding gas is essential.
- Gas Leakage Monitoring: Regularly monitor the gas supply system to ensure there are no leaks, which can lead to gas waste, safety risks, and welding quality issues.
- Backup Gas Sources: To ensure continuous welding operations, it’s recommended to have backup gas sources or cylinders in case of issues with the primary gas supply. This helps maintain production continuity.
- Gas Cost: Consider the cost of shielding gas. Some gases are more expensive than others, and balancing welding quality with cost savings is essential. In some cases, lower-cost gases can be used as auxiliary shielding gases to save on costs.
Proper supply and control of shielding gas are essential for the success of laser welding. By ensuring precise control of gas flow, pressure, and distribution, a stable atmosphere is provided, preventing oxidation and impurities from entering the welding area. Regular maintenance and monitoring of the gas supply system are necessary to maintain continuity and safety.
Conclusion
In the laser welding process, the selection, supply, and control of shielding gas are critical factors for achieving high-quality welding results. The choice of the right shielding gas is essential, and it should match the welding material, application requirements, and economic considerations. Proper gas flow control, distribution, and guidance ensure a stable atmosphere, preventing oxidation and impurities from compromising welding quality. Gas control systems play a vital role in highly automated processes.
Regular monitoring and maintenance of the gas supply system, along with the availability of backup gas sources, help maintain production continuity and safety. By considering these factors and collaborating with experts, laser welding engineers, and gas suppliers, the optimal shielding gas can be selected to meet specific requirements, ultimately leading to outstanding welding results.