Table of Contents
Laser cutting technology plays an increasingly crucial role in modern manufacturing, making the selection of a laser cutting machine that suits your specific needs a critical strategic decision for businesses. This article provides you with a comprehensive guide for purchasing a laser cutting machine, helping you navigate through the multitude of choices in the market and find the most suitable equipment.
1. Clear Cutting Requirements
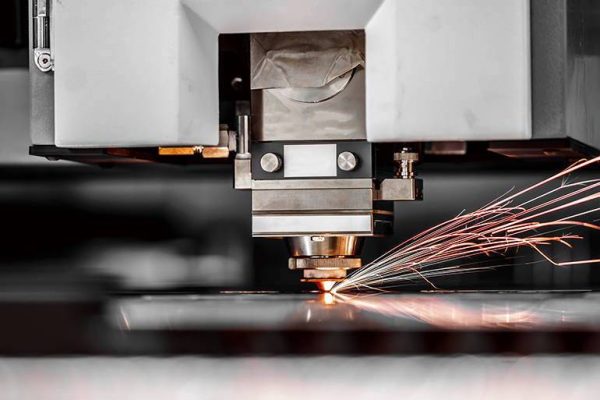
Before purchasing a laser cutting machine, it is essential to have a clear understanding of your cutting requirements. Determine the types of materials you primarily work with, the range of material thickness, and the quality standards for cutting. This helps narrow down the options and find a model that best fits your needs. When clarifying cutting requirements, consider not only the material type and thickness but also delve into production batch sizes and cutting frequencies. Understanding daily or weekly workloads assists in selecting the appropriate capacity and automation level of the laser cutting machine to meet practical needs.
2. Light Source Selection
Laser cutting machines have two main light sources: fiber laser and CO2 laser. Fiber lasers are suitable for metal cutting, while CO2 lasers are more applicable to non-metallic materials. The choice of the light source type should be based on the primary materials you cut. In addition to choosing between fiber and CO2 lasers, consider the brand and quality of the laser. Different laser brands may vary in energy efficiency, lifespan, and maintenance requirements. Thoroughly research the reputation and technological innovation of the light source manufacturer to ensure the selected laser cutting machine has a reliable light source.
More information about fiber and CO2 laser cutter can be found in in our article >> Fiber vs CO2 Laser Cutter: Which One Should You Choose?
3. Laser Power and Wavelength Selection
Deepen your understanding of how the laser power and wavelength of a laser cutting machine impact cutting results. Different powers and wavelengths are suitable for various cutting tasks, and selecting the right configuration enhances cutting quality. For different materials and cutting tasks, the choice of laser power and wavelength is crucial. Discuss various power and wavelength configurations with the supplier to ensure the selected laser cutting machine can adapt flexibly to different production requirements.
4. Material Compatibility and Cutting Speed Optimization
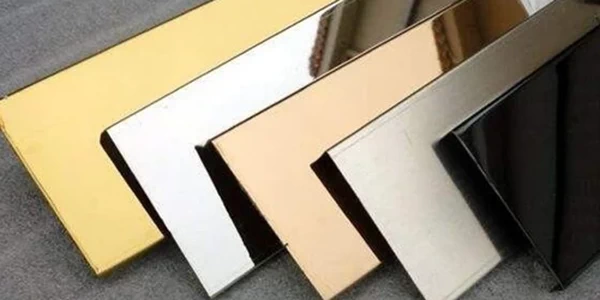
Consider the compatibility of the laser cutting machine with different materials, including various metals, plastics, wood, and more. Understand the machine’s cutting speed performance with different materials to optimize production efficiency. In addition to material compatibility, also consider whether the laser cutting machine has intelligent cutting parameter adjustment capabilities. Advanced models can automatically sense material properties and adjust cutting parameters in real-time to achieve the best cutting speed and quality.
5. Focus on Cutting Quality
Cutting quality is a crucial metric for evaluating laser cutting machine performance. Pay attention to the smoothness of cut edges, cutting accuracy, and cutting speed to ensure that the equipment meets your production quality standards. When focusing on cutting quality, request samples from the supplier to verify cutting quality on different materials and thicknesses. Additionally, understand whether the equipment has real-time detection and feedback mechanisms and whether cutting parameters can be fine-tuned through software.
6. Cutting Head Design and Adjustment Mechanism
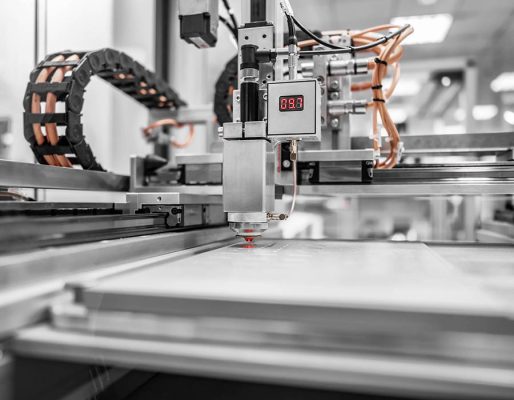
Before purchasing a laser cutting machine, it is essential to have a clear understanding of your cutting requirements. Determine the types of materials you primarily work with, the range of material thickness, and the quality standards for cutting. This helps narrow down the options and find a model that best fits your needs. When clarifying cutting requirements, consider not only the material type and thickness but also delve into production batch sizes and cutting frequencies. Understanding daily or weekly workloads assists in selecting the appropriate capacity and automation level of the laser cutting machine to meet practical needs.
7. Automation Level and Intelligence
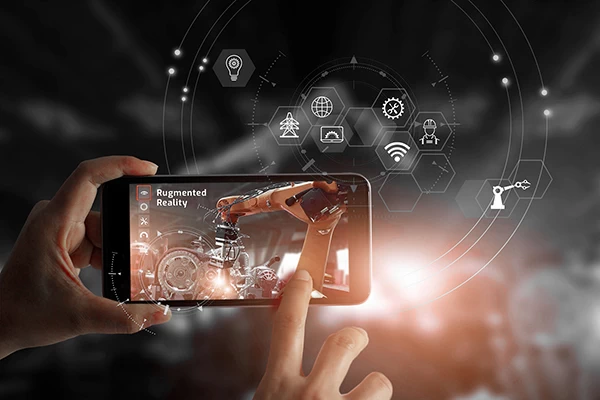
Highly automated laser cutting machines can improve production efficiency and reduce the need for manual intervention. Intelligent control systems and user interfaces also reduce operational complexity, enhancing the machine’s user-friendliness. Consider whether the laser cutting machine supports data-driven production for digitized management of the production process. Additionally, remote monitoring features can improve real-time monitoring and fault diagnosis capabilities.
8. Auxiliary Gases in Laser Cutting
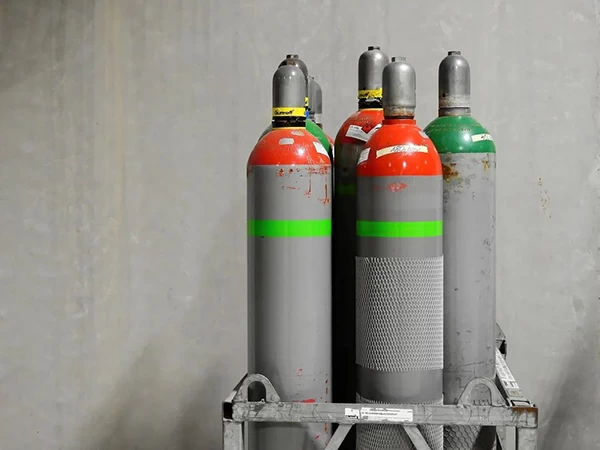
Thoroughly research the auxiliary gas used during cutting, such as nitrogen, oxygen, etc. Understand their impact on cutting results and how to adjust gas parameters to meet the requirements of different materials. In addition to considering the type of auxiliary gas, find out whether the laser cutting machine supports a multi-gas cutting system. Different gases have different effects on the cutting results for specific materials, and having this flexibility allows better adaptation to different production needs.
To learn more about auxiliary gases for laser cutting, you can read this article >> How to Choose Auxiliary Gas for Laser Cutting?
9. Laser Cutting Machine Cooling System
Understand the laser cutting machine’s cooling system, especially for machines with high-power laser sources. An effective cooling system helps maintain equipment stability and extend its lifespan. Gain detailed insights into the design and performance of the cooling system, especially its performance under high-power laser sources. An effective cooling system not only keeps the equipment running stably but also helps reduce energy consumption and maintenance costs.
10. After-Sales Service and Support
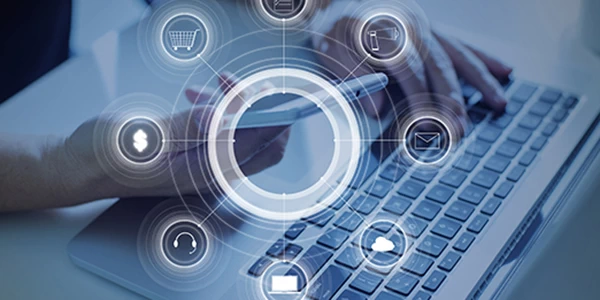
Choosing a manufacturer that provides excellent after-sales service and technical support is crucial. Timely maintenance and support ensure the long-term stable operation of the equipment, reducing the impact of potential faults. Communicate with the manufacturer about their after-sales service plan, including regular maintenance, emergency repair response time, and parts supply. Find out if there is online support and training services to ensure your team can operate and maintain the laser cutting machine proficiently.
11. Equipment Space Requirements and Layout
The space requirements and layout of the laser cutting machine in the factory or workshop are also factors to consider when making a purchase. Ensure that the equipment can adapt to the actual production environment without affecting other workflow processes. When considering equipment space requirements, look beyond the machine’s dimensions to consider the requirements for the surrounding working space. Understand the flexibility of the equipment’s layout to ensure seamless integration into the production process.
12. Energy Consumption and Environmental Considerations
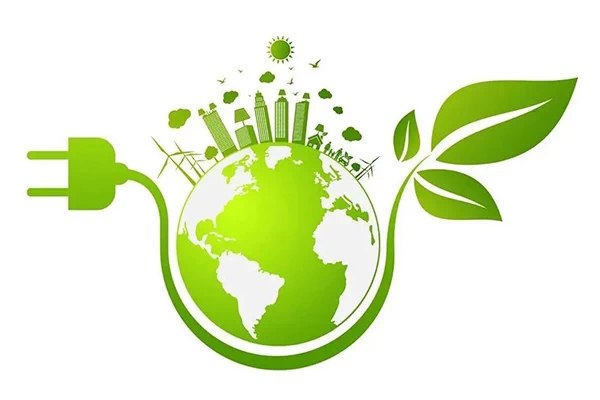
Focus on the energy consumption of the laser cutting machine, choosing equipment with high efficiency to reduce operating costs. Environmental awareness is also an essential consideration, and selecting equipment that meets environmental standards is crucial. Delve into the equipment’s energy consumption details, especially its efficiency performance in different working modes. Choosing a laser cutting machine compliant with energy standards helps reduce operating costs while enhancing environmental credibility.
13. Manufacturer Reputation and History
Choosing a manufacturer with a good reputation and rich history often indicates that their products have withstood market tests. Explore user reviews, visit production facilities, and check customer cases and industry recognition to understand the manufacturer’s reputation in the laser cutting field. Visiting the production facility provides a firsthand experience of the manufacturer’s production processes and quality control standards, ensuring that the selected equipment comes from a trusted manufacturer.
14. Cost and Budget Control
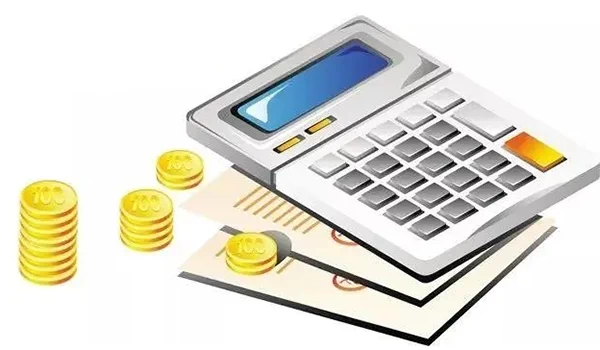
Comprehensively consider the overall cost of purchasing a laser cutting machine, including acquisition costs, operating costs, and maintenance costs. Ensure that the equipment fits within your budget while not compromising on quality and performance. When considering costs, focus not only on the purchase cost but also on the operational and maintenance costs of the equipment. Discuss long-term cost plans with the manufacturer, understanding potential additional fees to ensure the equipment aligns with your overall budget.
15. Safety and Compliance
As a high-energy device, safety is a crucial factor in the purchase decision for a laser cutting machine. Ensure that the equipment complies with local and international safety standards and regulations, including machine safety standards, laser radiation safety standards, and operator safety standards. Additionally, understand whether the equipment is equipped with necessary safety features such as emergency shutdown systems, protective cover designs, and audible and visual alarm systems. Regularly train operators to increase their awareness and skills in safely operating the laser cutting machine, minimizing potential safety risks.
16. Future Upgradability
When considering future upgradability, focus on whether the laser cutting machine supports flexible upgrades of both software and hardware. Understand whether the manufacturer provides options for later upgrades to accommodate potential business expansions or technological advancements. This may involve upgrading the laser source, updating the control system, or improving automation components. Choosing equipment with good upgradability can extend its lifespan, reduce future upgrade costs, and ensure that the equipment remains synchronized with the latest industry technologies.
Conclusion
By thoroughly considering these 16 key factors, you will be able to make informed decisions and choose a laser cutting machine that best suits your needs, injecting powerful cutting capabilities into your manufacturing industry. During the purchasing process, pay attention not only to the basic parameters of the equipment but also engage in detailed discussions with the manufacturer to understand the details and performance of the equipment, ensuring that your investment achieves maximum efficiency in production. The choice of a laser cutting machine not only relates to current production needs but also requires consideration of future development directions. Therefore, making rational and comprehensive purchasing decisions will bring long-term competitive advantages to your business. If you have any further questions or need more detailed information, feel free to consult with us to ensure that your laser cutting machine investment delivers the expected results. Wishing you outstanding achievements in the field of laser cutting!