Table of Contents
Laser cutting technology occupies an important position in modern manufacturing, providing the possibility to achieve high-precision and high-efficiency cutting. The selection of suitable auxiliary gases is crucial to ensuring cutting quality and improving cutting efficiency in the laser cutting process. This article will provide a detailed overview of the auxiliary gases commonly used in laser cutting for various materials.
1. Role of Auxiliary Gases in Laser Cutting
Laser cutting, known for its high precision and efficiency in material processing, relies significantly on the role of auxiliary gases. The functions of auxiliary gases extend beyond clearing melted materials; they also influence cutting quality, stabilize the cutting process, and enhance cutting speed. Here are the main roles of auxiliary gases in laser cutting:
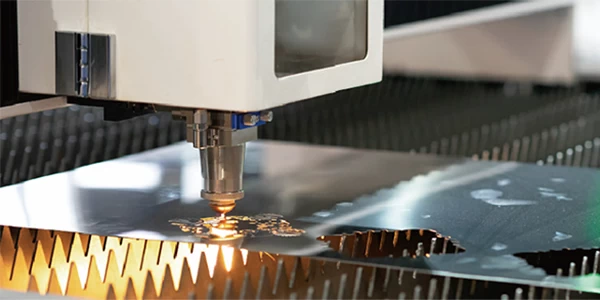
1.1 Removal of Molten Material
The high energy of the laser beam causes instant melting of the material, forming a molten pool. Auxiliary gases, when directed into the cutting area, swiftly blow away the molten metal and debris, ensuring the laser beam can continue cutting the material unobstructed. This clearing action is crucial for maintaining the accuracy of the cutting line and overall cutting quality.
1.2 Stabilizing the Cutting Process:
Auxiliary gases in laser cutting also play a role in cooling and stabilizing the laser focus. By cooling the molten pool, these gases help prevent excessive heat concentration, thereby preventing material deformation and improving cutting precision. Additionally, they assist in maintaining the focus of the laser beam within the cutting area, ensuring clarity and consistency of the cutting line.
1.3 Preventing Oxidation Reactions
In laser cutting, some metals are prone to oxidation reactions at high temperatures, affecting cutting quality. Using inert gases such as nitrogen or argon as auxiliary gases effectively prevents oxidation, especially in cutting materials like stainless steel, copper, and aluminum, which are susceptible to oxidation.
1.4 Impact on Cutting Quality
Different auxiliary gases have varying effects on cutting quality. For example, oxygen is commonly used for cutting carbon steel, enhancing cutting speed but potentially causing oxidation. Nitrogen is suitable for cutting materials like stainless steel, improving cutting quality. Therefore, when selecting auxiliary gases, it’s essential to make a rational choice based on specific materials and requirements.
1.5 Increasing Cutting Speed
The choice of auxiliary gases is closely related to cutting speed. By controlling the flow and pressure of auxiliary gases, the removal speed of material during cutting can be adjusted, thereby influencing overall cutting speed.
In practical applications, a thorough understanding and utilization of the roles of auxiliary gases, combined with a reasonable selection based on specific materials and cutting requirements, are crucial for ensuring the stability, efficiency, and quality of the laser cutting process.
2. Main Types of Auxiliary Gases
To ensure complete combustion, avoid residue, and protect components such as mirrors during laser cutting, auxiliary gases are essential for assisting combustion. Considering processing costs and specific working conditions, common auxiliary gases include oxygen, nitrogen, air, and argon. The following briefly analyzes the suitable processing environments for each gas.
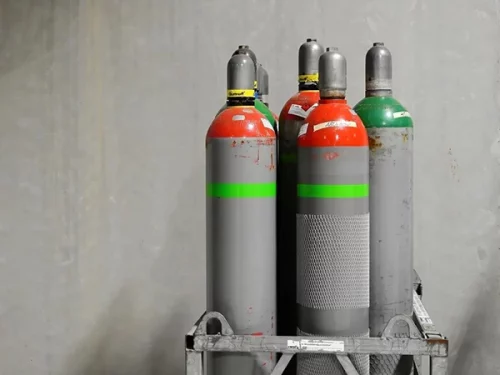
2.1 Air
Air is the most basic auxiliary gas for processing, with almost no usage cost other than compression. Air mainly consists of 78% nitrogen, 21% oxygen, and small amounts of other gases. The relatively low concentration of oxygen in air helps prevent the cutting surface from turning black. By compressing air, pressure, flow rate, and airflow quality can be safely controlled to adjust processing effects promptly. However, air processing lacks additional acceleration effects and does not provide surface protection.
Air has the widest application range and can be used for metals such as carbon steel, stainless steel, aluminum alloys, as well as non-metal materials like wood and acrylic. Moreover, the risk factor of using compressed air is relatively low.
2.2 Oxygen
Oxygen is suitable as an auxiliary for metal processing. Providing an adequate amount of oxygen can also enhance combustion, making the processing point burn more fully and improving efficiency. It is the fastest processing gas among all auxiliary gases. Using high-speed oxygen can help residues detach from the metal, alleviating slagging and blackening issues.
For carbon steel, low-alloy steel materials, or processing thicker plates, or when quality and surface requirements are not high, oxygen can be considered as an auxiliary. However, when using high-concentration oxygen, attention should be paid to safety, handling it with care and keeping it away from sources of ignition and laser heat sources.
2.3 Nitrogen
Nitrogen-assisted processing has some special advantages. Nitrogen prevents oxidation reactions, blows away melted materials, maintains relative cooling of the workpiece, and keeps the cutting surface as clean as new, resulting in superior cutting quality.
Nitrogen processing is more suitable for cutting materials like stainless steel. However, it is essential to note that nitrogen needs to be produced using an industrial nitrogen generator, and its storage is less convenient than oxygen. Additionally, the nitrogen consumption per unit time is usually higher than oxygen, potentially increasing the overall cost of nitrogen processing.
2.4 Argon
Argon is an inert gas used in laser cutting to prevent oxidation and nitridation, also used in welding. Argon helps protect the cutting appearance and is more effective in reducing the heat-affected zone. However, as an inert gas, argon is difficult to prepare, and its cost is higher. It is generally used for processing special materials such as titanium alloys and copper.
3. Common Auxiliary Gases for Different Metal Materials
Handheld laser welding exhibits excellent applicability in thin plate welding and can be used for various types of thin plate materials, including but not limited to stainless steel, aluminum alloy, titanium alloy, etc. This versatility has led to widespread applications in industries such as electronics, automotive, medical instruments, and more.
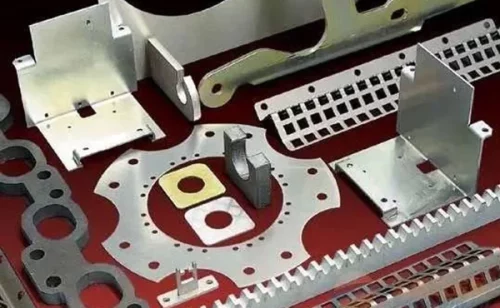
3.1 Carbon Steel
For laser cutting of carbon steel, oxygen is generally used. Oxygen cutting can be divided into positive focus cutting and negative focus cutting. The section of positive focus cutting is bright or matte, and when using high-power equipment, negative focus cutting can be adopted. The quality of the cutting section of medium-thick plates is slightly inferior, but the cutting speed is fast and efficient. For thin plates, nitrogen or air can be used for cutting, resulting in extremely high efficiency. It is essential to note that when cutting carbon steel plates with nitrogen or air, the thicker the material, the more burrs may be present.
3.2 Stainless Steel
Laser cutting of stainless steel commonly uses nitrogen or air. The cutting effects of these two gases differ, with nitrogen cutting resulting in a silver-white section, while air cutting shows a yellow-black section. Additionally, because air contains oxygen, which has a combustion-assisting effect, cutting speed with air is often faster than with nitrogen.
3.3 Aluminum Alloy
Laser cutting of aluminum alloys typically uses nitrogen or air. The sections cut by both gases are silver-white. Nitrogen cutting of aluminum plates does not produce oxidation reaction. However, since aluminum itself is silver-white, although air cutting has oxidation, the oxidized aluminum oxide is also white. It should be noted that the cutting speed of aluminum plate is faster than that of stainless steel.
3.4 Galvanized Sheet
Laser cutting of galvanized sheets typically uses nitrogen or air, employing the same cutting principles as cutting stainless steel.
3.5 Brass
Laser cutting of brass typically uses nitrogen or air, employing the same cutting principles as cutting stainless steel.
3.6 Copper
Copper is a highly reflective material, and during laser cutting, high-pressure oxygen is usually employed. Copper undergoes partial oxidation with oxygen, helping reduce laser reflection back into the laser.
3.7 Titanium Alloy
Laser cutting of titanium alloy typically uses air, which is the most economically effective choice. However, if you want to maintain the original metallic color of the titanium alloy, choosing an inert gas like argon for cutting is recommended, but this will increase costs.
3.8 Composite Board
For composite boards with one side made of stainless steel and the other side made of carbon steel, air is typically used for cutting. The cutting principles are the same as cutting stainless steel, with the carbon steel side facing up and the stainless steel side facing down.
3.9 Special Metal Materials
For high-hardness special metal materials, attempting air cutting is an option. Due to the high hardness of these materials, cutting speed may be slower, and specific speeds need to be determined based on hardness. If air cutting is ineffective, high-pressure oxygen cutting can be attempted. However, if all the above methods fail, traditional processing methods may be the only solution.
4. Considerations for Auxiliary Gas Selection
In laser cutting, choosing the appropriate auxiliary gas is a crucial step in ensuring cutting effects and process stability. The selection of auxiliary gases is influenced by various factors, and the following are important considerations:
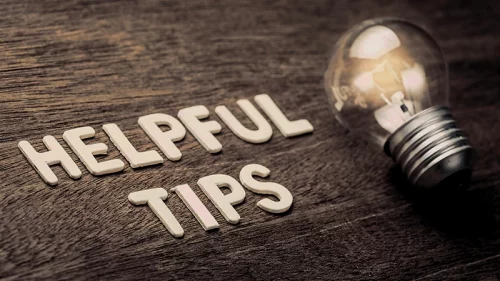
4.1 Material Characteristics
- Metal Type: Different metals react differently to auxiliary gases. For example, oxygen performs well in cutting carbon steel but is unsuitable for metals prone to oxidation, such as copper and aluminum. For materials like stainless steel, nitrogen or other inert gases are typically chosen.
- Material Thickness: Material thickness also affects the selection of auxiliary gases. Thicker materials may require larger gas flow rates and pressures to ensure effective clearing and cooling.
4.2 Cutting Speed and Quality Requirements
- Cutting Speed: Different auxiliary gases can impact cutting speed. Oxygen, for example, can increase cutting speed but might compromise cutting quality in some situations. For applications requiring high-speed cutting, oxygen may be a preferred choice.
- Cutting Quality: If higher cutting edge quality is required, selecting gases that produce a clear and smooth cutting edge, such as nitrogen or argon, is essential.
4.3 Cost Factors
- Gas Costs: Different auxiliary gases have varying costs, which may be influenced by market fluctuations. Balancing cutting quality and costs is crucial to ensuring the selected gas aligns with economic considerations.
- Efficiency Improvement: Despite higher costs for some auxiliary gases, if significant improvements in cutting efficiency can be achieved, it may lead to more significant long-term savings.
4.4 Safety Considerations
- Gas Stability: The stability of auxiliary gases during the cutting process needs to be considered to prevent potential accidents.
- Operator Safety: Some gases may pose risks, such as oxygen being combustible. Proper safety measures should be taken during use to ensure the safety of operators.
4.5 Environmental Considerations
- Waste Gas Treatment: Different auxiliary gases may produce varying amounts of waste gas. In applications with high environmental requirements, the disposal of waste gases needs to be considered when choosing gases.
4.6 Special Application Requirements
- Special Metals: For cutting special metals like titanium alloys, selecting more suitable auxiliary gases is necessary to ensure cutting quality.
- High Precision Requirements: Applications with high precision requirements may necessitate finer gas control to ensure cutting accuracy.
By considering the factors mentioned above, ensuring the selected auxiliary gas meets specific application requirements, and adjusting the choice of auxiliary gases flexibly in different cutting scenarios, the laser cutting process can achieve optimal results in terms of cutting efficiency, quality, and cost-effectiveness.
5. Conclusion
In conclusion, laser cutting is a key process in modern manufacturing, and the selection of auxiliary gases directly impacts cutting effects and process stability. When choosing the appropriate auxiliary gas, it is crucial to consider material characteristics, cutting speed and quality requirements, cost factors, safety considerations, environmental factors, and any special application requirements. Different application scenarios may require flexible adjustments to the choice of auxiliary gases to meet specific production needs. For practitioners in the manufacturing industry, carefully selecting suitable auxiliary gases will become an indispensable part of ensuring the successful application of laser cutting processes.