Table of Contents
The CO2 laser cutting machine, also known as the carbon dioxide laser cutting machine, is primarily used in the laser cutting of non-metallic materials in the current market. This article focuses on introducing the working principles, technical advantages, application areas, factors influencing cutting quality, and future development trends of CO2 laser cutting machines.
Working Principles of CO2 Laser Cutting Machine
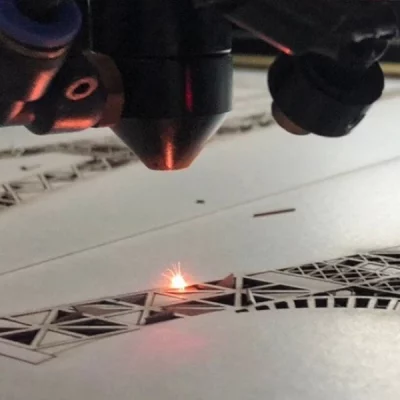
The working principles of the CO2 laser cutting machine involve generating a laser within the excited cavity filled with CO2 gas. By introducing electric current or an electron beam into this cavity, CO2 molecules are excited to a high-energy state, resulting in laser generation. The initially weak laser is then amplified through gain media, such as a mixture of nitrogen and helium gases, to increase laser intensity.
The generated and amplified laser is focused precisely through an optical system, including lenses and mirrors, forming a laser beam with extremely high energy density. This laser beam is directed to the cutting area, interacting with the material. In the cutting zone, the high energy density of the laser causes localized heating of the material, leading to instantaneous melting or vaporization, achieving a high-precision and efficient cutting process. These processes make the CO2 laser cutting machine a powerful and flexible cutting tool in industrial production.
The laser wavelength of the CO2 laser cutting machine is 10.6 micrometers, stable, and has an energy conversion efficiency of up to 25%. Many organic materials exhibit strong absorption of this long wavelength, making CO2 laser cutting machines widely applied in industries such as paper, wood, plastics, rubber, textiles, and leather.
Advantages of CO2 Laser Cutting Machine
The CO2 laser cutting machine is a common laser cutting device with numerous advantages. The main advantages of the CO2 laser cutting machine include:
High Precision
The CO2 laser cutting machine achieves very high cutting precision, enabling millimeter-level precision cutting on various materials, including metals, plastics, wood, textiles, and more.
Narrow Kerf
The laser beam is focused into a small spot, reaching high power density at the focus, rapidly heating the material to the gasification point. As the beam linearly moves relative to the material, it forms a narrow cut with a width generally between 0.10 to 0.20 mm.
Smooth Cutting Surface
The cutting surface is free from burrs, and the roughness of the cut is generally controlled within Ra12.5.
High Speed
CO2 laser cutting machines exhibit fast cutting speeds, allowing them to complete a large number of cutting tasks in a short time. They enable efficient production, improving production efficiency significantly compared to traditional cutting methods.
Excellent Cutting Quality
With non-contact cutting, minimal heat affects the cutting edge, resulting in minimal workpiece deformation. There is almost no edge collapse formed during material shearing, and the cut does not require secondary processing.
No Workpiece Damage
The laser cutting head does not come into contact with the material surface, ensuring no scratches on the workpiece.
Not Affected by Material Hardness
Capable of processing materials such as steel, stainless steel, aluminum alloy, and hard alloys without being affected by their hardness.
Not Influenced by Workpiece Shape
Flexible and suitable for processing any shape, including pipes and other profiles.
Cutting of Non-Metallic Materials
Capable of cutting non-metallic materials such as plastic, wood, PVC, leather, textiles, and organic glass.
Saves Mold Investment
Eliminates the need for molds, reduces mold consumption and repair time, saving processing costs, especially suitable for large product processing.
Material Saving
Computer programming allows for the nesting of different-shaped products on a whole sheet, maximizing material utilization.
Applications of CO2 Laser Cutting Machine
Due to its high precision, fast cutting speed, and smooth cutting surface, the CO2 laser cutting machine is well-suited for cutting and processing non-metallic materials, including wood, acrylic, rubber, plastic, leather, textiles, and more. Here are some of its main applications.
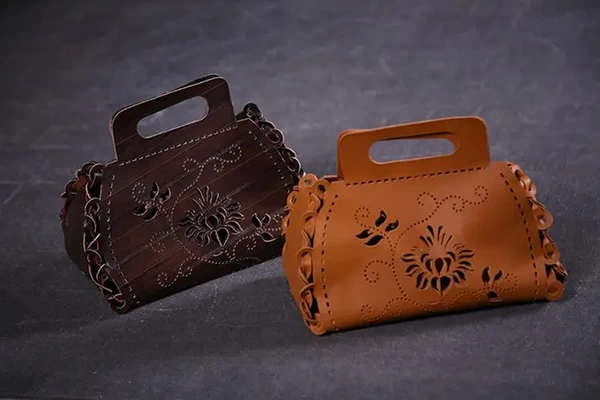
Leather Cutting
Using CO2 laser cutting for leather creates intricate patterns, adding a sense of design to products. With high precision and clean cutting sections, CO2 laser cutting provides a neat texture to the overall product. Traditional cutting machines often create defects along the edges during plate cutting, resulting in slow speeds, less smooth surfaces, and lower precision. The advent of laser cutting machines quickly revolutionized the traditional cutting market.
Paper Cutting
CO2 laser cutting allows for more intricate patterns on paper, discarding square shapes. Whether cutting out city skyline contours in the air or creating a three-dimensional fantasy forest, desired effects can be achieved simply by using a laser cutting machine. Even in complex and detailed paper art pieces, the current laser cutting machines enable rapid realization of the intended results.
Wood Cutting
In addition to leather, CO2 laser cutting is suitable for various materials such as fabric, acrylic, wooden boards, rubber, and more. The laser-cut wood lampshades below demonstrate the excellent precision achieved through laser cutting. Laser-cutting wood provides exceptional accuracy, producing elegant and delicate effects with clear, neat patterns.
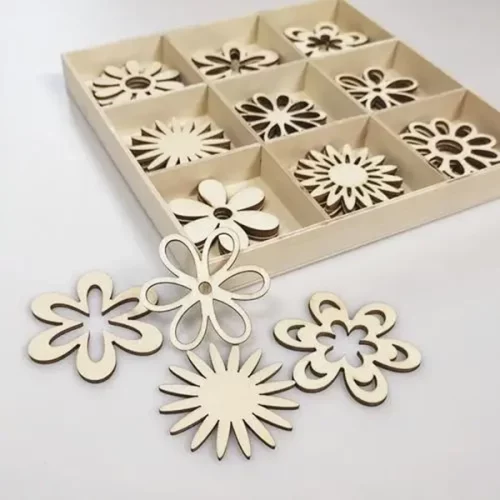
Compared to traditional cutting techniques, laser cutting machines impose no mechanical stress, resulting in superior product effects, precision, and cutting speed. Computer-designed graphics can cut out any shape, pattern, or size of lace, offering high efficiency and low cost. These are significant advantages of laser cutting compared to traditional processing methods.
Factors Affecting CO2 Laser Cutting Machine Cutting Quality
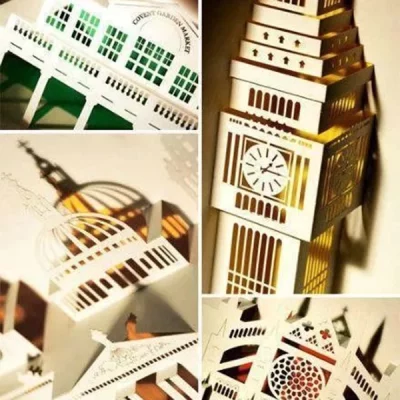
The quality of cutting directly affects production costs. Factors influencing the cutting quality of CO2 laser cutting machines include:
Laser Power and Stability
Different powers yield different thicknesses in laser cutting. Setting the maximum power in practical operations often aims to reduce cutting time or cut thicker materials. However, daily production observations have found that the highest power density is obtained at the focus under less than maximum power conditions, resulting in the best cutting quality. Besides power size, power stability is crucial. Continuous production poses a significant challenge to laser power stability, especially for direct current-excited laser cutters due to electrode erosion leading to power decay.
Auxiliary Gas Pressure
In laser cutting, auxiliary gas serves to remove melted and evaporated materials from the cutting area, preventing excessive burning. When cutting thicker materials, the gas pressure should be reduced, and for thinner materials, it should be increased to prevent residue from sticking on the back of the cut. Gas pressure adjustments also depend on the material being cut. For instance, when cutting plastic, lower pressure is preferable to prevent frosting on the edges.
Laser Frequency
Laser output can be pulsed or continuous. Lasers used for cutting and welding mainly adopt pulse output. Pulse frequency significantly influences cutting speed and cut roughness. High-frequency pulsing is essential for achieving high-speed cutting. Currently, most manufacturers produce carbon dioxide lasers with frequencies within 5000Hz.
Beam Divergence Angle
While beam divergence angle technically does not belong to the laser part, it significantly affects the far-field divergence angle due to the laser's mode heavily influencing it. Smaller beam divergence angles result in narrower cut widths and smaller slopes, leading to higher quality.
Future Development Trends
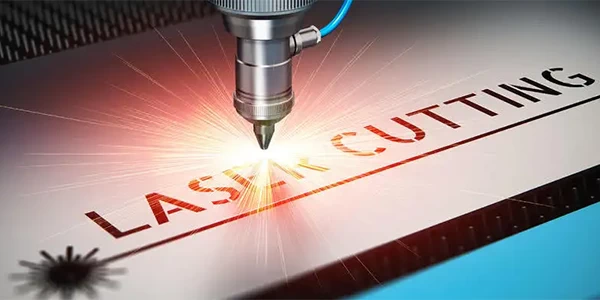
While the current use of CO2 laser cutting machines primarily focuses on non-metallic materials, they still lag behind fiber laser cutting machines when it comes to cutting metal products. As an advanced manufacturing technology, the future development of CO2 laser cutting machines covers various aspects, from technological innovation to the expansion of widespread applications:
Higher Power
Future CO2 laser cutting machines are expected to achieve higher power, further improving cutting speed and capacity to meet broader manufacturing demands.
Increased Intelligence
With the development of artificial intelligence and machine learning technologies, CO2 laser cutting machines are expected to achieve more intelligent and adaptive control systems, enhancing cutting precision and efficiency.
Expanded Material Selection
Through technological innovation, future CO2 laser cutting machines are expected to broaden their applicability to more types of materials, including new composite materials and ceramics.
Wider Industry Applications
With ongoing technological advancements, CO2 laser cutting machines will find more applications in emerging fields such as medical, electronics, aerospace, further consolidating their position in the industrial sector.
3D Laser Cutting
In future trends, CO2 laser cutting machines may integrate more 3D laser cutting technology to address more complex structures and design requirements.
Green and Sustainable Development
With an increased awareness of environmental protection, future CO2 laser cutting machines may focus more on green and sustainable design, reducing energy consumption and environmental impact.
In conclusion, the future development trends of CO2 laser cutting machines will primarily revolve around improving technical performance, expanding application areas, achieving higher levels of intelligence, and focusing on environmental sustainability. These trends aim to meet the growing demands of the manufacturing industry for efficient, precise, and sustainable production.
Conclusion
The CO2 laser cutting machine is an efficient tool widely used in the cutting of non-metallic materials. In practical applications, CO2 laser cutting machines have demonstrated excellent performance across multiple industries. The future development trends indicate ongoing innovation and expansion of application areas for CO2 laser cutting machines. Overall, the CO2 laser cutting machine, with its characteristics of efficiency, precision, and wide adaptability, not only drives progress in modern industry but also shows significant potential for innovation and application in the future.