Table of Contents
Laser welding technology, as a high-precision and efficient welding method, has been widely used in the manufacturing industry. However, there are instances where we may encounter the problem of weak laser output in laser welding machines, which can be caused by various factors. This article will delve into the possible reasons for weak laser output in laser welding machines and provide solutions to ensure the normal operation of the equipment.
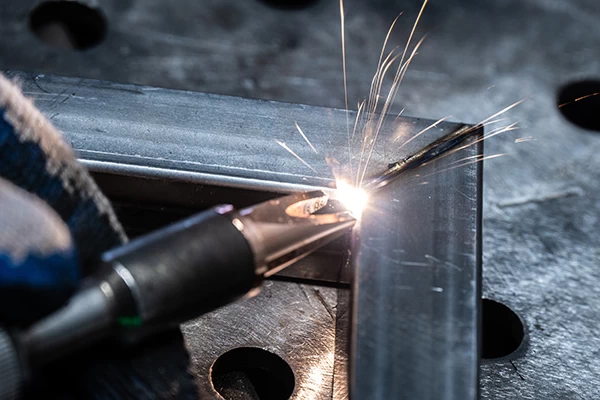
Causes of Weak Laser Output in Laser Welding Machines
The causes of weak laser output can vary, primarily including issues with the laser source, beam transmission losses, insufficient power of the light source, and environmental factors.
Laser Source Malfunction
Internal components of the laser source may get damaged due to prolonged use, high temperatures, or other factors. Detailed laser source diagnostics are required in such cases, and it may involve replacing damaged components or calibrating the laser source. Different materials and processes require different beam qualities, so it’s crucial to choose an appropriate laser source and ensure it maintains a high-quality beam output. Regular checks on the laser source’s beam quality and adjustments or replacements of optical components are essential.
Beam Transmission Losses
Transmission losses in the laser beam path can also result in weak laser output during welding. During laser transmission, the beam passes through various optical components such as lenses and mirrors. These components may cause scattering, absorption, and reflection of the beam, leading to energy loss. The losses become more severe when there is dirt, oxidation, or damage on the surfaces of these optical components.
Insufficient Power of the Light Source
Insufficient power of the light source is a major cause of weak laser output in laser welding. The welding process requires a significant amount of energy to heat and melt the workpiece. If the light source power is inadequate, it cannot provide enough energy to complete the welding process. Insufficient light source power may result from equipment aging, lens wear, unstable power supply, or hardware/software failures in the control system. Therefore, regular checks and maintenance of laser welding equipment to ensure sufficient light source power are crucial.
Mismatched Material Absorption Rates
The absorption rate of materials during laser welding is a critical factor affecting welding light intensity. Different materials have different absorption rates for laser beams, with some materials having lower absorption rates, requiring higher laser energy for welding. If the chosen laser power does not match the material’s absorption rate, it can lead to weak welding light. Therefore, accurate testing of material absorption rates before laser welding and selecting the appropriate laser power based on test results are necessary to ensure sufficient welding light intensity.
Environmental Factors
Laser welding processes may be affected by environmental factors such as temperature, humidity, and gases. Laser welding needs to be conducted under specific environmental conditions. If the temperature is too high or too low, humidity is too high or too low, or harmful gases are present, it can negatively impact the laser welding process and lead to weak light output. Therefore, controlling environmental conditions appropriately before laser welding is essential.
Methods to Solve Weak Laser Output in Laser Welding Machines
When facing the issue of weak laser output in laser welding machines, it is crucial to adopt comprehensive and effective solutions. The following are in-depth solutions to help correct the weak light output of laser welding machines:
1. Laser Source Maintenance
Regular maintenance of the laser source is key to preventing weak light output. Maintenance steps include cleaning the cooling system, checking for aging and damage to internal components of the laser source, and adjusting laser source power according to production requirements. Establishing detailed maintenance logs helps track changes in laser source performance.
2. Optical System Optimization
Use high-quality optical components, ensure their surfaces are clean, and perform regular calibrations of the optical system. Implement an automated adjustment system that can monitor and adjust the positions of optical components in real-time, ensuring accurate and stable focus.
3. Control Parameter Adjustments
Evaluate the requirements of the welding task and adjust parameters in the control system accordingly. Gradually adjust power, frequency, and pulse width based on material characteristics, welding depth, and speed, ensuring that light output meets expectations.
4. Intelligent Control System
Introduce an intelligent control system that monitors the performance data of the laser source and optical system in real-time, automatically adjusting control parameters. Such a system can respond quickly to changes, improve production efficiency, and reduce the occurrence of weak light output issues.
5. Advanced Monitoring Technologies
Combine advanced monitoring technologies such as infrared thermal imaging and laser beam quality analysis for comprehensive performance monitoring of laser welding machines. Real-time detection of anomalies allows for timely identification and resolution of issues in the laser source and optical system.
Preventive Measures for Weak Laser Output in Laser Welding Machines
To avoid the problem of weak laser output in laser welding machines, several preventive measures can be taken:
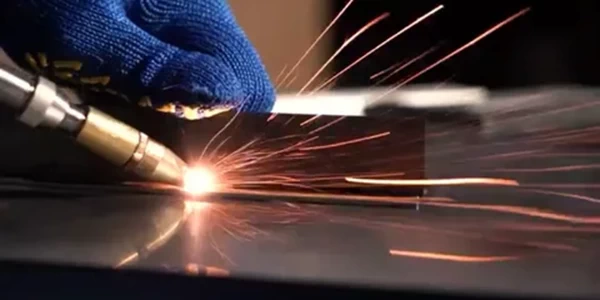
Environmental Control
Ensure laser equipment is in suitable environmental conditions. Control temperature and humidity to avoid adverse effects on laser source lenses. Environmental control measures, such as moisture, dust, and shock prevention, effectively reduce external factors' damage to laser source lenses.
Safety Operating Procedures
Establish strict operating procedures, including startup and shutdown operations, cleaning, and maintenance processes. Train operators to understand correct operating methods and precautions, reducing the risk of lens damage due to improper operation.
Use of Protective Covers
Install protective covers or devices to shield laser source lenses from mechanical damage or external impact. This helps prevent scratches, collisions, or other unforeseen events from affecting the lens surface.
Regular Inspections
Develop a regular inspection plan for laser source lenses. Periodically check and clean the lenses, and use optical tests to monitor transmittance and reflectance, promptly identifying and addressing potential issues.
Optical Coating Protection
Choose optical coatings with high wear resistance and high transmittance to extend the life of lenses. These special coatings provide pollution resistance and scratch resistance, slowing down the aging process of the lens surface.
Standardized Cleaning Methods
Adhere to correct cleaning methods using suitable cleaning agents and tools to ensure lens surfaces are not damaged during cleaning. Use non-fiber, non-abrasive cleaning cloths to avoid scratches due to improper cleaning.
Regular Replacements
According to the recommendations of laser source manufacturers, establish a reasonable replacement cycle. Regularly replace lenses, even in cases where tiny damages are imperceptible to the naked eye, to prevent a gradual decline in laser output quality. In handheld laser welding, lenses are usually the most frequently replaced components. For damage prevention, it is advisable to use original manufacturer lenses, be cautious about contamination during replacement, and avoid vertical welding, especially when welding high-reflectance materials.
Record Keeping and Maintenance Logs
Maintain detailed maintenance logs, recording the time, steps, and results of each cleaning, inspection, and replacement. This helps track the usage of laser source lenses and facilitates the timely establishment of corresponding maintenance plans.
By comprehensively implementing these preventive measures, the lifespan of laser source lenses can be maximized, reducing the occurrence of weak light output issues, and ensuring that laser welding machines maintain good performance and stability in production.
Summary
Solving the issue of weak laser output in laser welding machines requires a multi-faceted approach, including addressing laser source conditions, optimizing optical system performance, and adjusting control system parameters. Through comprehensive management and preventive measures, the stability and performance of laser welding machines can be effectively ensured, enhancing production efficiency and product quality.